- Bespoke Shoes Unlaced - The Journal
- Posts
- Journal Issue 7 : New Craft of Shoemaking Award : Open City : London Design Festival
Journal Issue 7 : New Craft of Shoemaking Award : Open City : London Design Festival
A glimpse into our shoemaking world
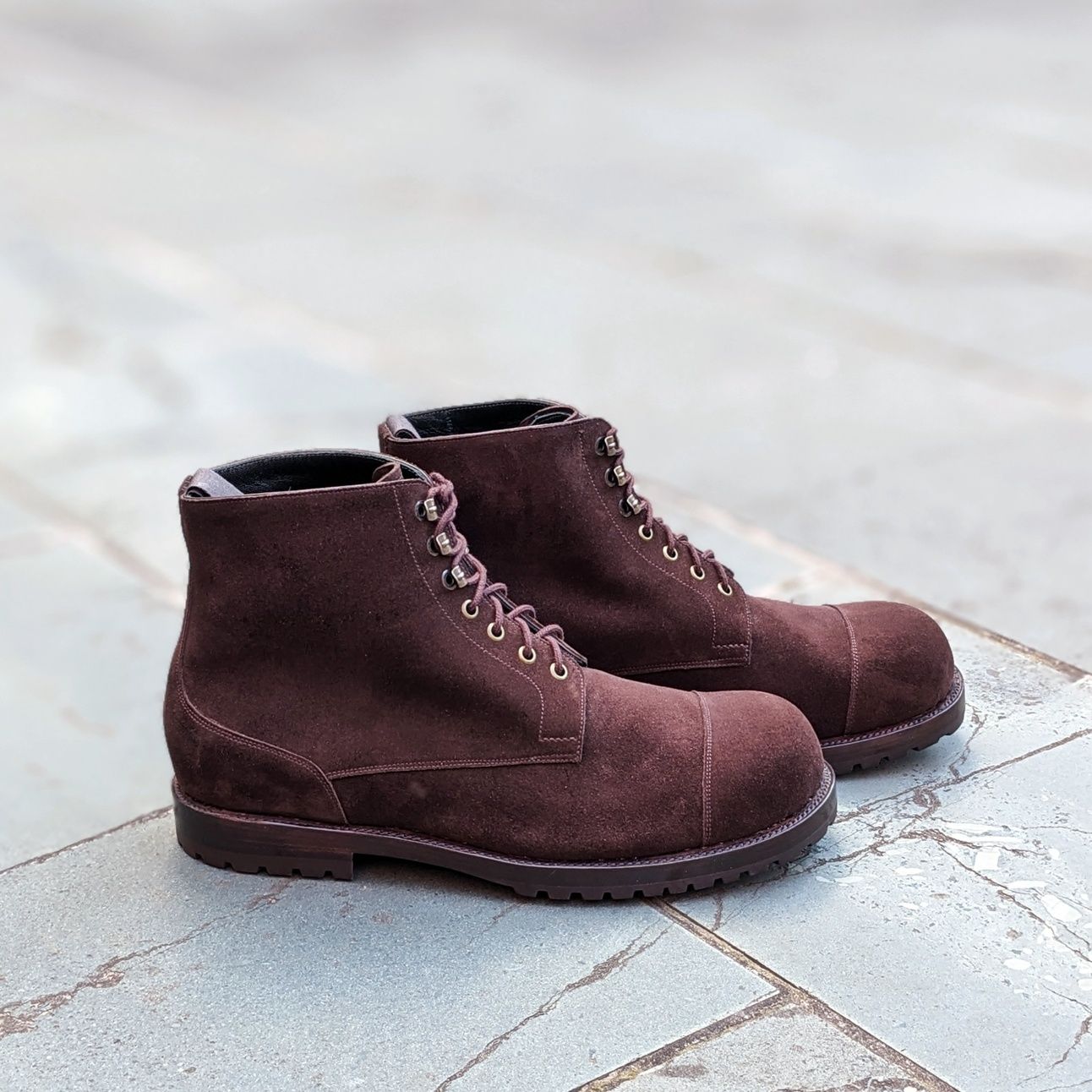
JOURNAL 7
AWARD Launch : DECOREX : Open House + London Design Festival
In our second autumn issue we’re looking back at a packed September - with Open City London, London Design Festival and Decorex - and we’re looking forward to announcing a new Award in conjunction with the Worshipful Company of Cordwainers, the Craft of Shoemaking Award alongside our regulars, Bespoke Shoe of the month, In the Workshop and Tool of the month.
Enjoy!
Deborah & James
NEW Craft of Shoemaking Award
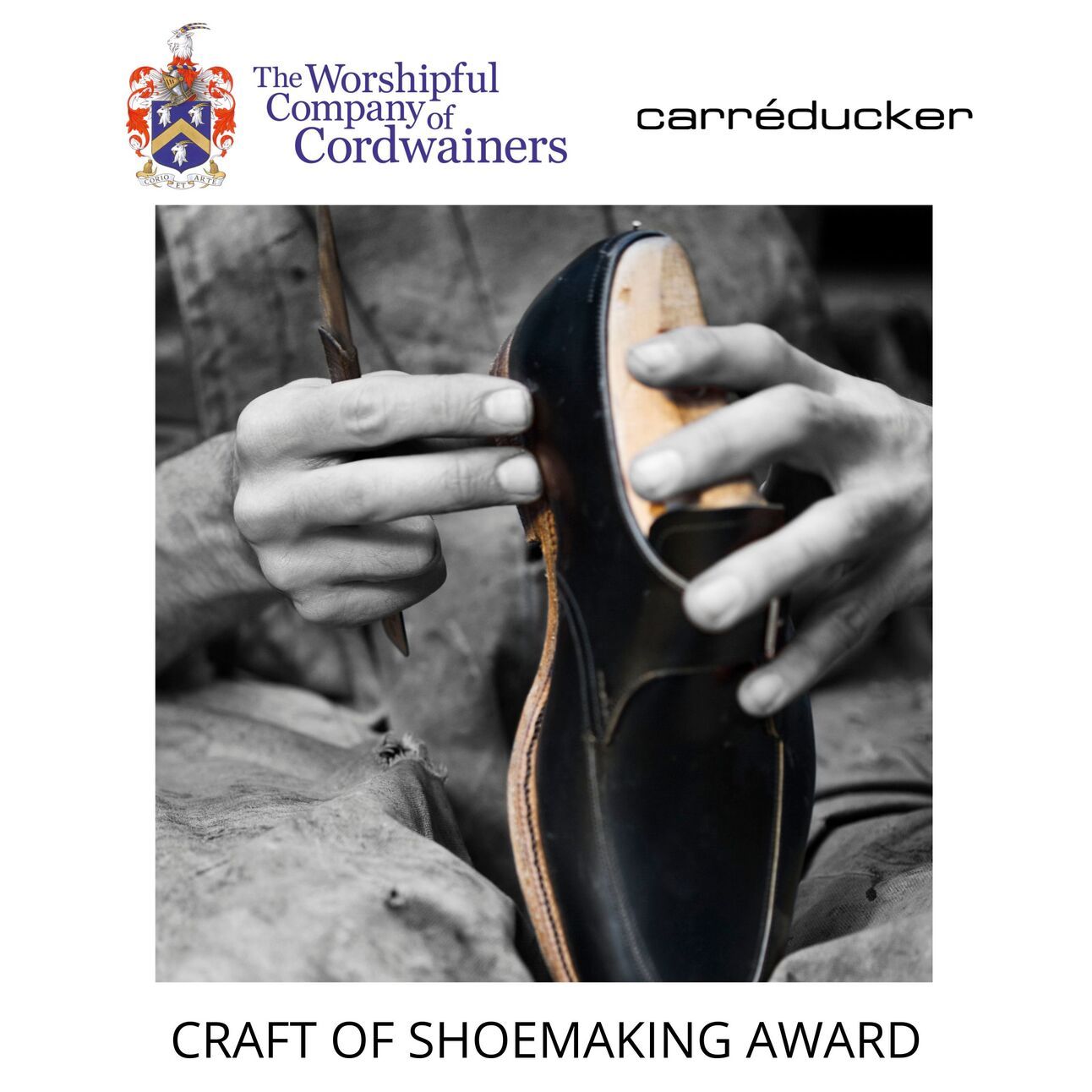
Photo by Richard Boll
We’ve long felt that shoemaking has played second fiddle to its sexier cousin shoe design, perhaps because it requires investment in equipment and specialist training or because it’s easier to see a career path into the footwear industry as a designer than as a shoemaker. (Big shout out to Capel Manor for its making focused shoemaking course; to DMU for bringing in Trickers’ bespoke shoemaker, Adele Williamson to continue Bill Bird’s shoemaking training there; and to LCF for bringing in Georgina Goodman to lead its shoe course!)
But not all shoemakers need to end up as sole traders or piece workers working out of their garden shed or attic. There are endless opportunities for someone who understands the process of constructing a shoe and working with leather, not just in shoemaking or shoe manufacturing but in leatherwork, upholstery, furniture etc.
Those industries need to play their part by showing makers where their skills can be applied. Making skills are transferable - think about that hand eye coordination, tool dexterity, material knowledge, muscle memory, visualisation etc.
So we’re delighted to be launching a new award for shoe MAKERS with the Worshipful Company of Cordwainers, the Craft of Shoemaking Award.
It’s aimed at apprentices, students and vocational practitioners (where you’re not yet selling your shoes) based here in the UK. You are invited to make a pair of shoes with a focus on handskills and can work with anyone you like to make them, you just need to declare their involvement in your submission.
The winner will receive some 100 hours of training - developing closing and pattern making techniques with Fiona Campbell and handsewn shoemaking techniques with us!
We hope that you will enter. If you have any questions, please get in touch and if you would like to borrow a pair of lasts to make on we’d be more than happy to help.
DECOREX / OPEN HOUSE / LONDON DESIGN FESTIVAL
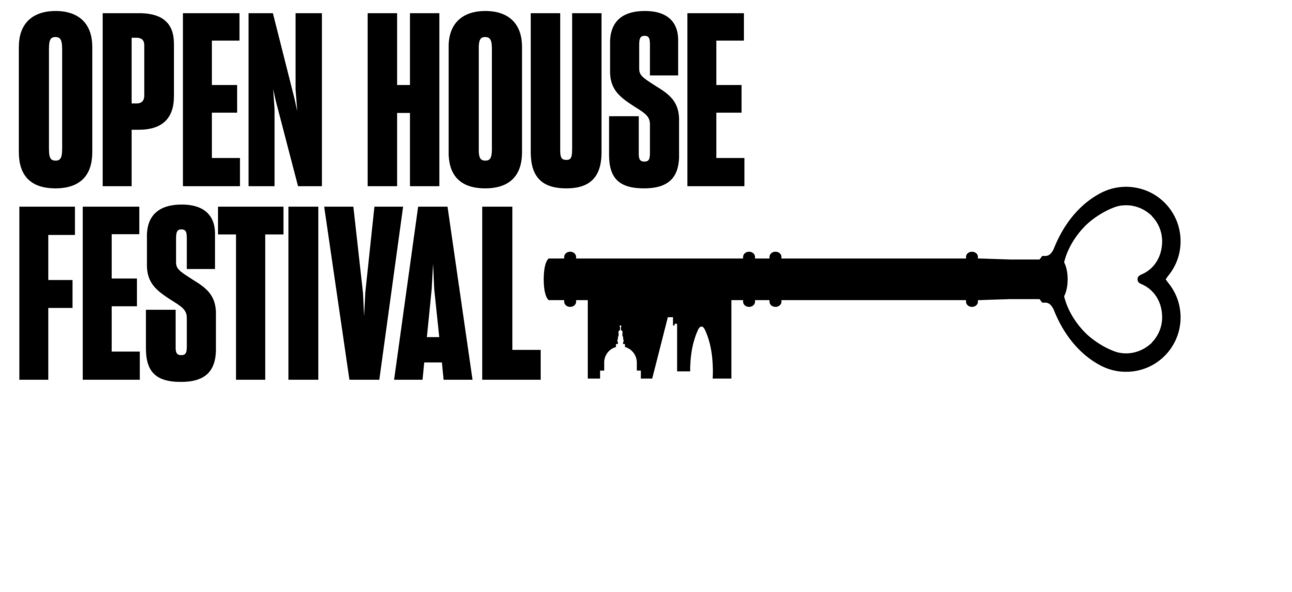
We had some lovely groups in our drop-in key fob making workshops, including three generations of the same family
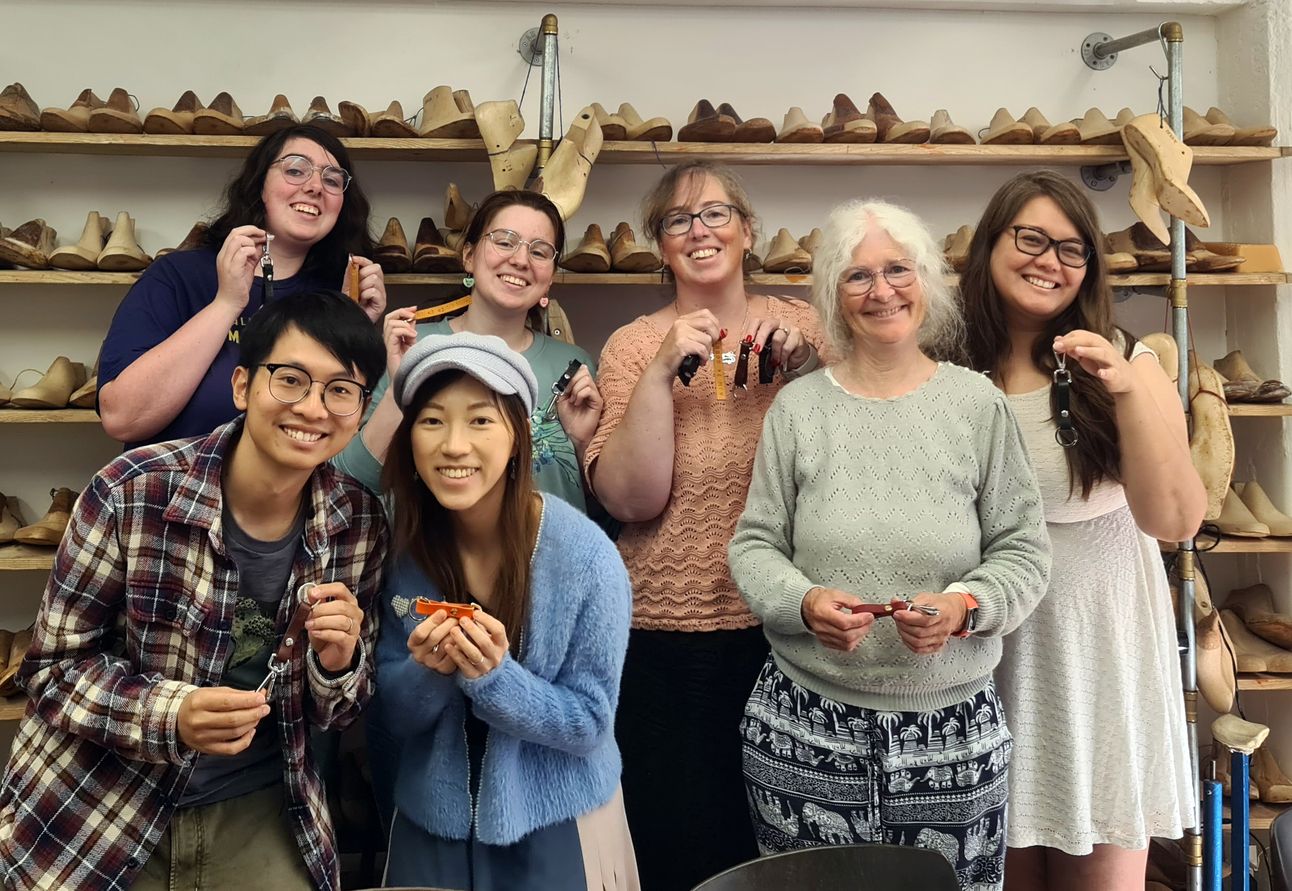
…but also took the leap of doing a talk!
As newly appointed Freemen of the Worshipful Company of Cordwainers we thought it would be interesting to discover more about the cordwainers of yore. So we did a heap of research and put together a presentation that walks through the lives of London shoemakers from the 13th century right up to the present day, along with a little social history to put the ups and downs of cordwaining life into perspective.
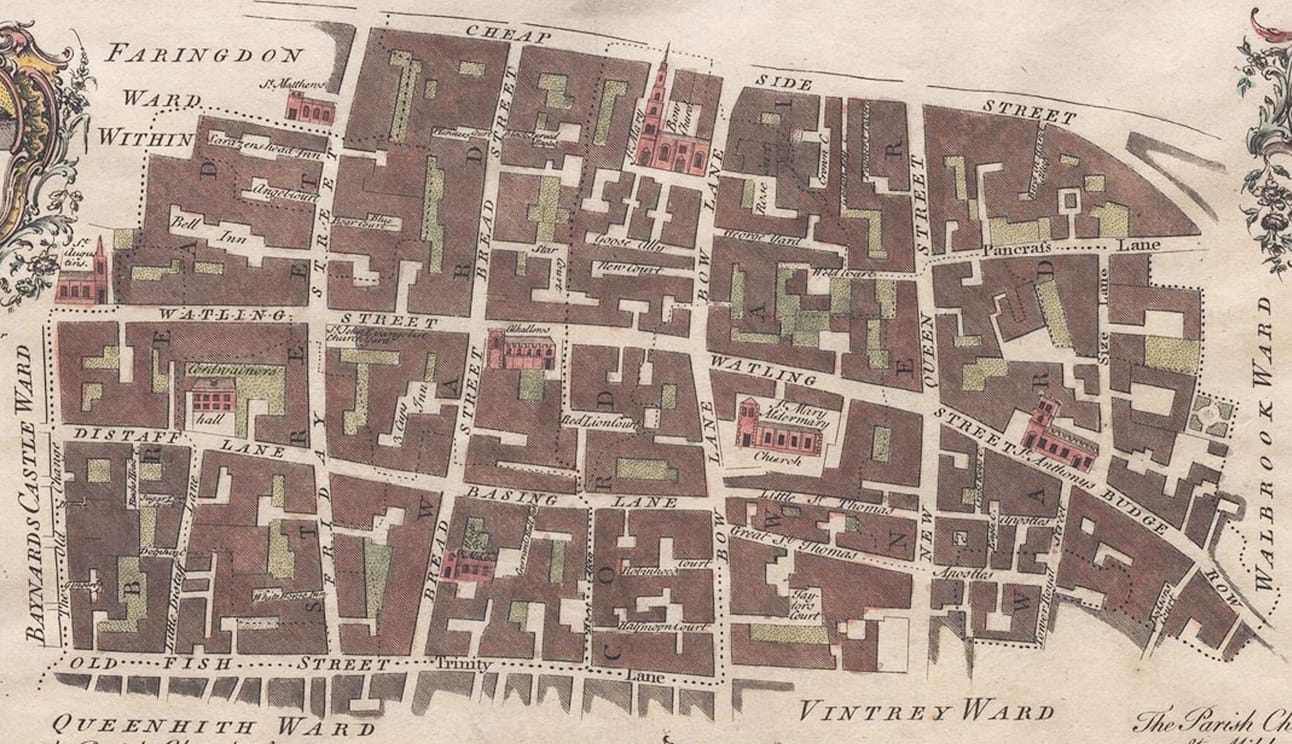
Cordwainer ward in the City of London 1755
It was a bit of a squeeze to get an audience into the workshop, along with the projector, projection screen and of course the worktable, but if there’s one thing we’ve become adpet at it’s squeezing a lot of stuff into a very small space. And bless them, our lovely audiences seemed to enjoy it!
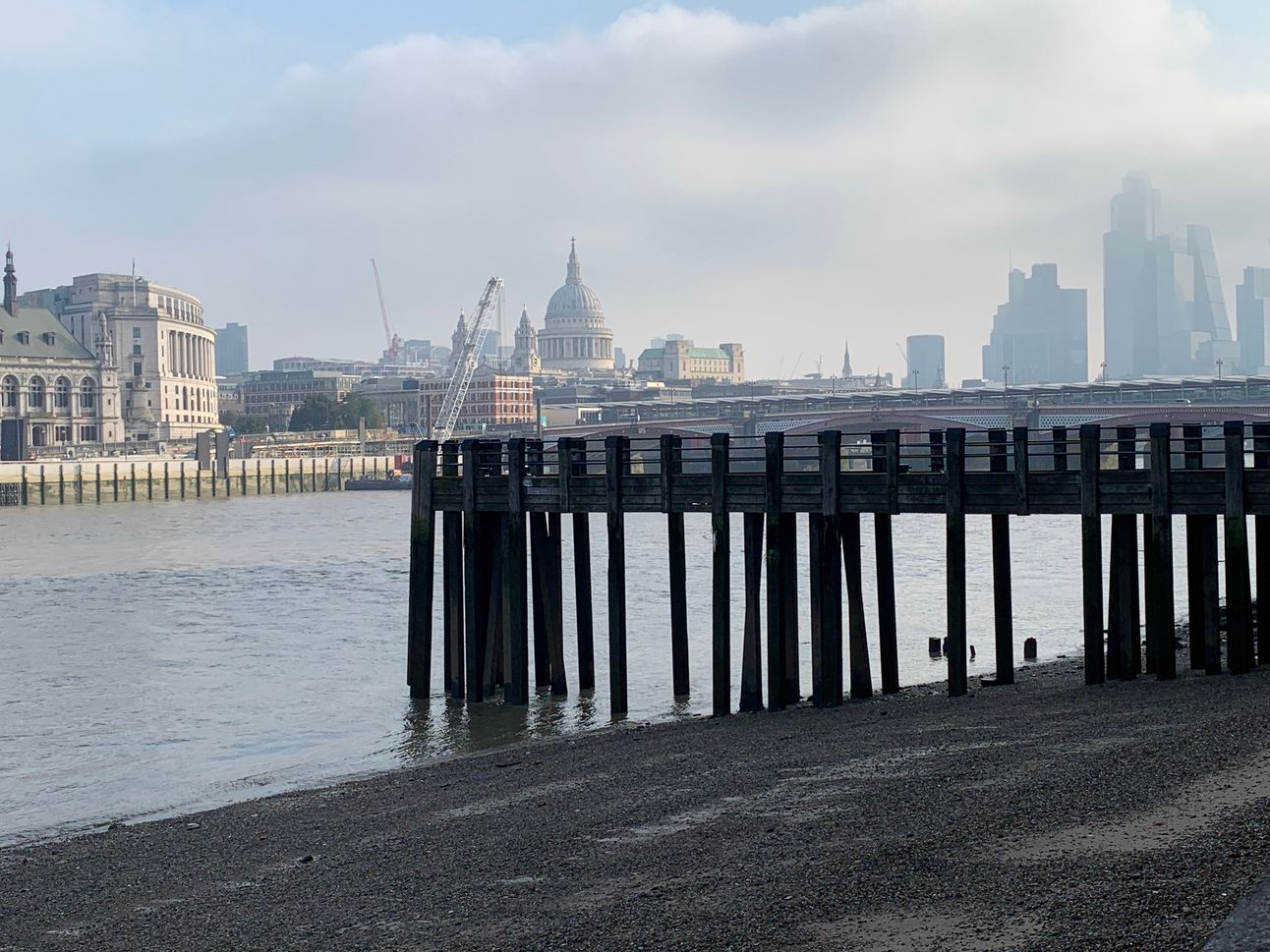
Looking towards St Pauls on the edge of Cordwainers Ward
So if you’re looking for after dinner speakers with a unique story to tell, call our agent!
LONDON DESIGN FESTIVAL
Hot on the heels of Open House is the London Design Festival. As James was having a well-earned break in Italy - feasting on gelato, limoncello and pasta - I took the opportunity to bring in some leather work to showcase in the studio for Oxo Tower Wharf’s late night shopping evening. Thanks to everyone who came in for a drink and to chat vegetable tanned leather!
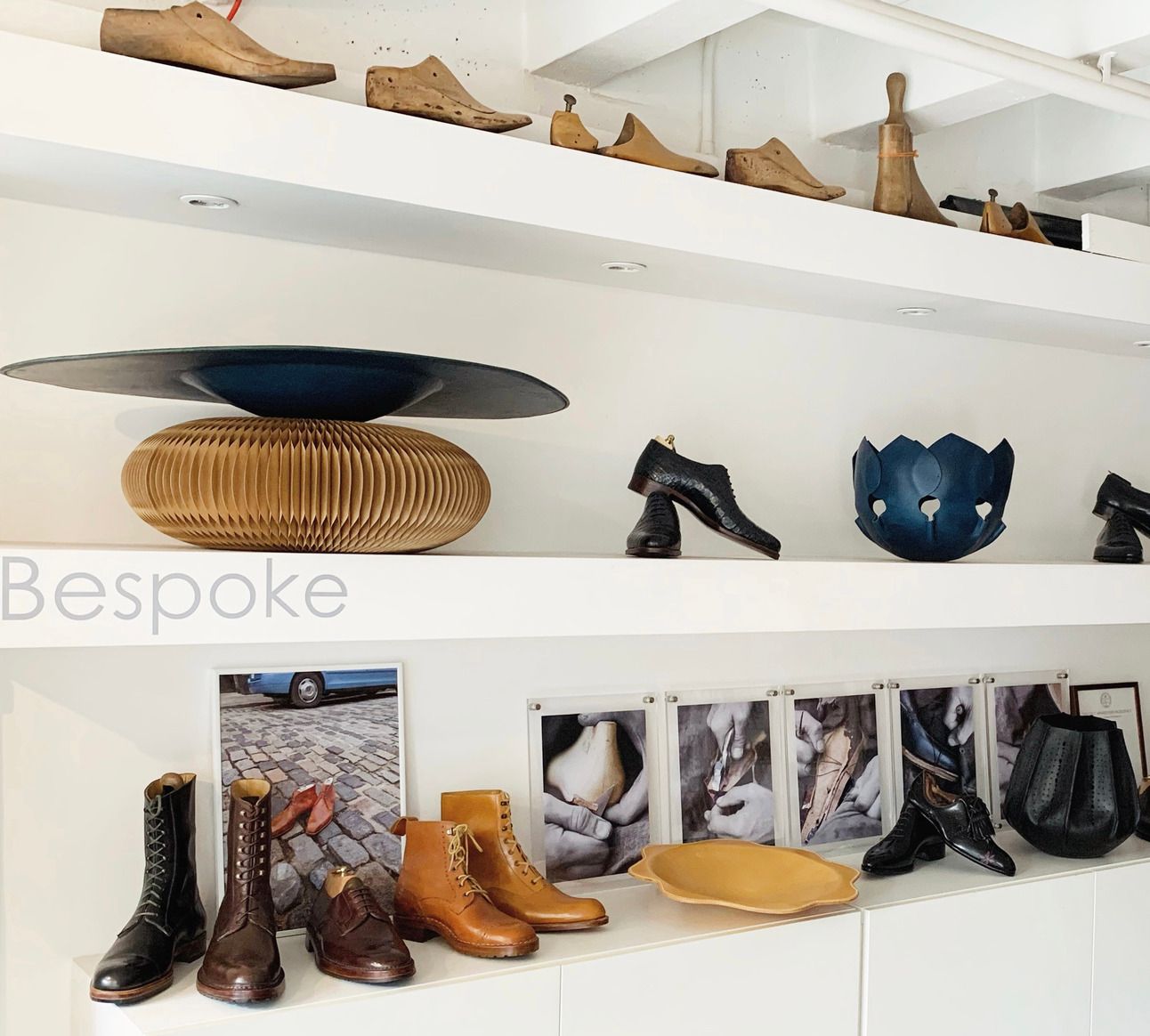
Wet moulded vessels and bespoke footwear crafted using similar tools and skills
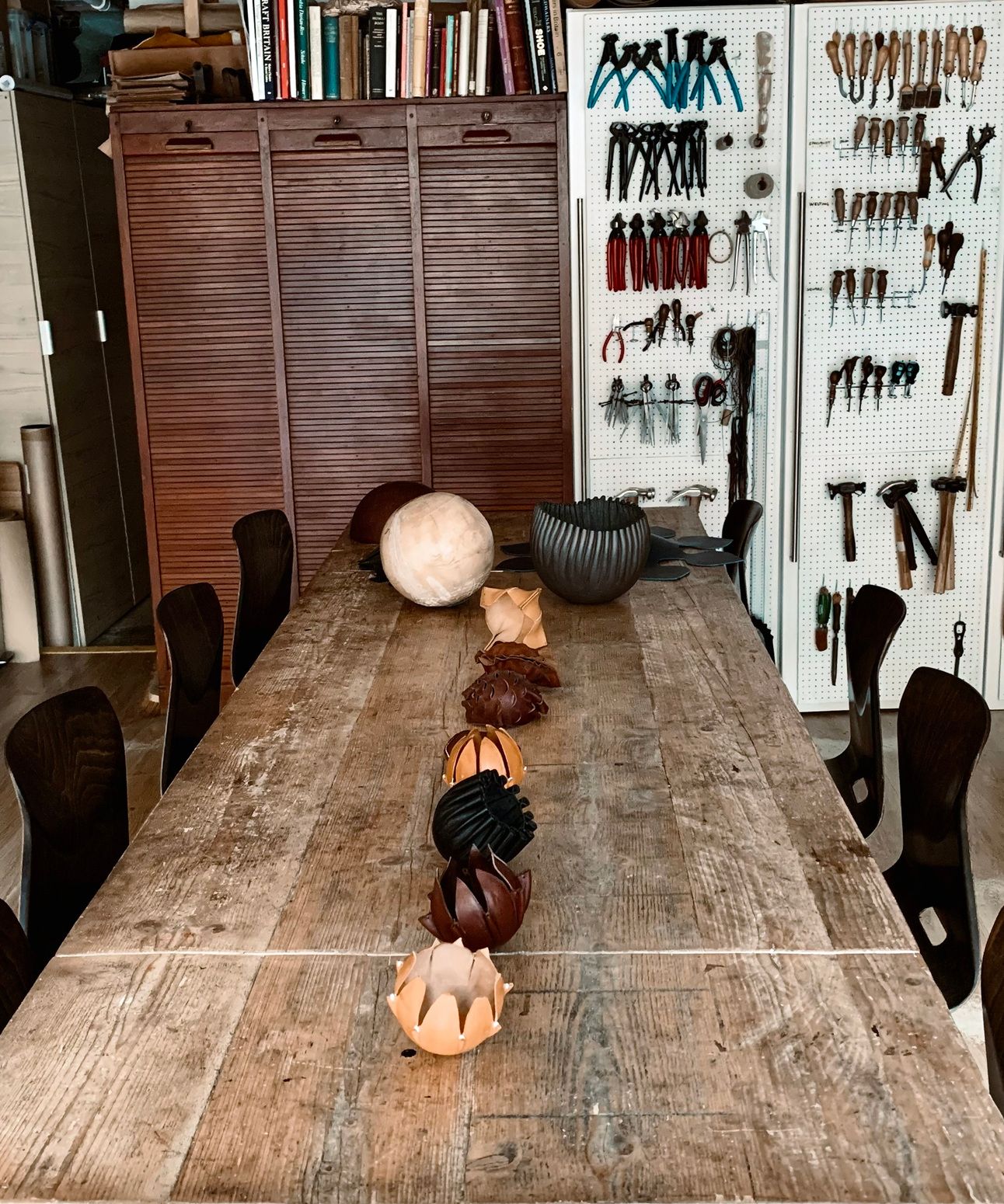
The evolution of my pod series inspired by nature
You can see more about my process and why I started making vessels in this short by film graduate Nathan Walker
DECOREX
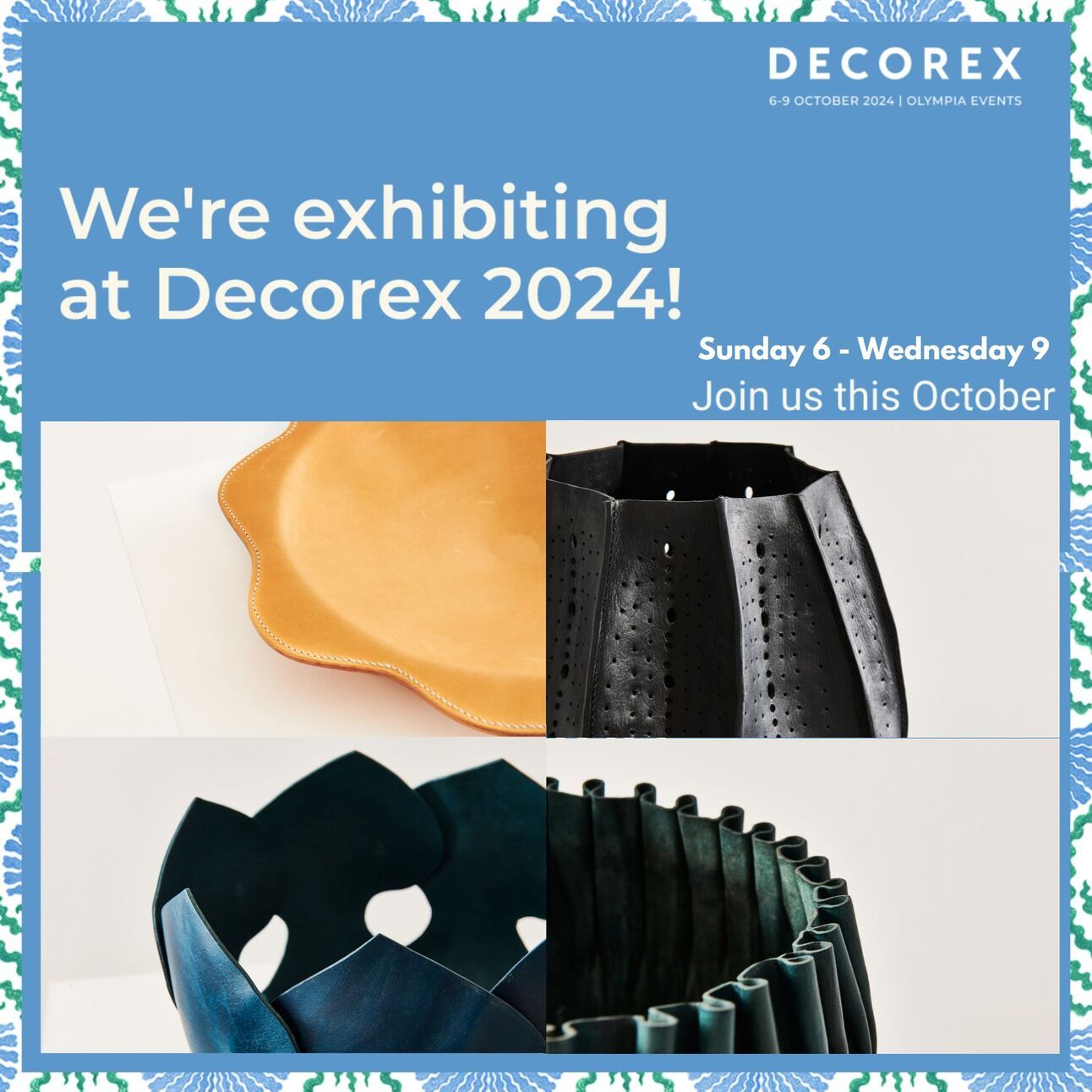
As you can see, the start of autumn is always a busy one, but it was made all the more so this year as I was invited to exhibit at DECOREX Making Spaces, (massive thanks to Future Icons for the noimination). It’s a four-day trade show for the best of interior decoration and design.
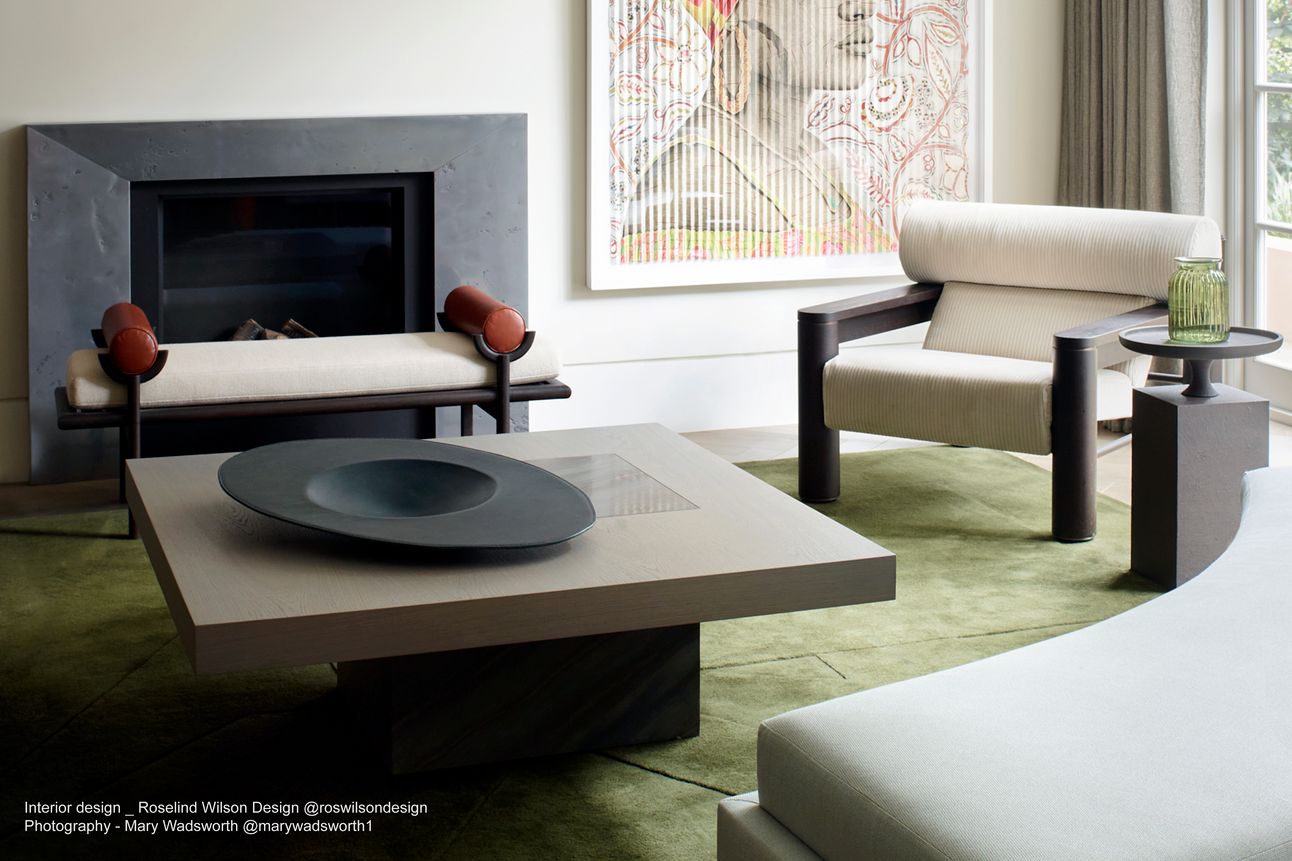
This is my leather vessel, Gravity, photographed by Mary Wadsworth for Rosalind Wilson Design
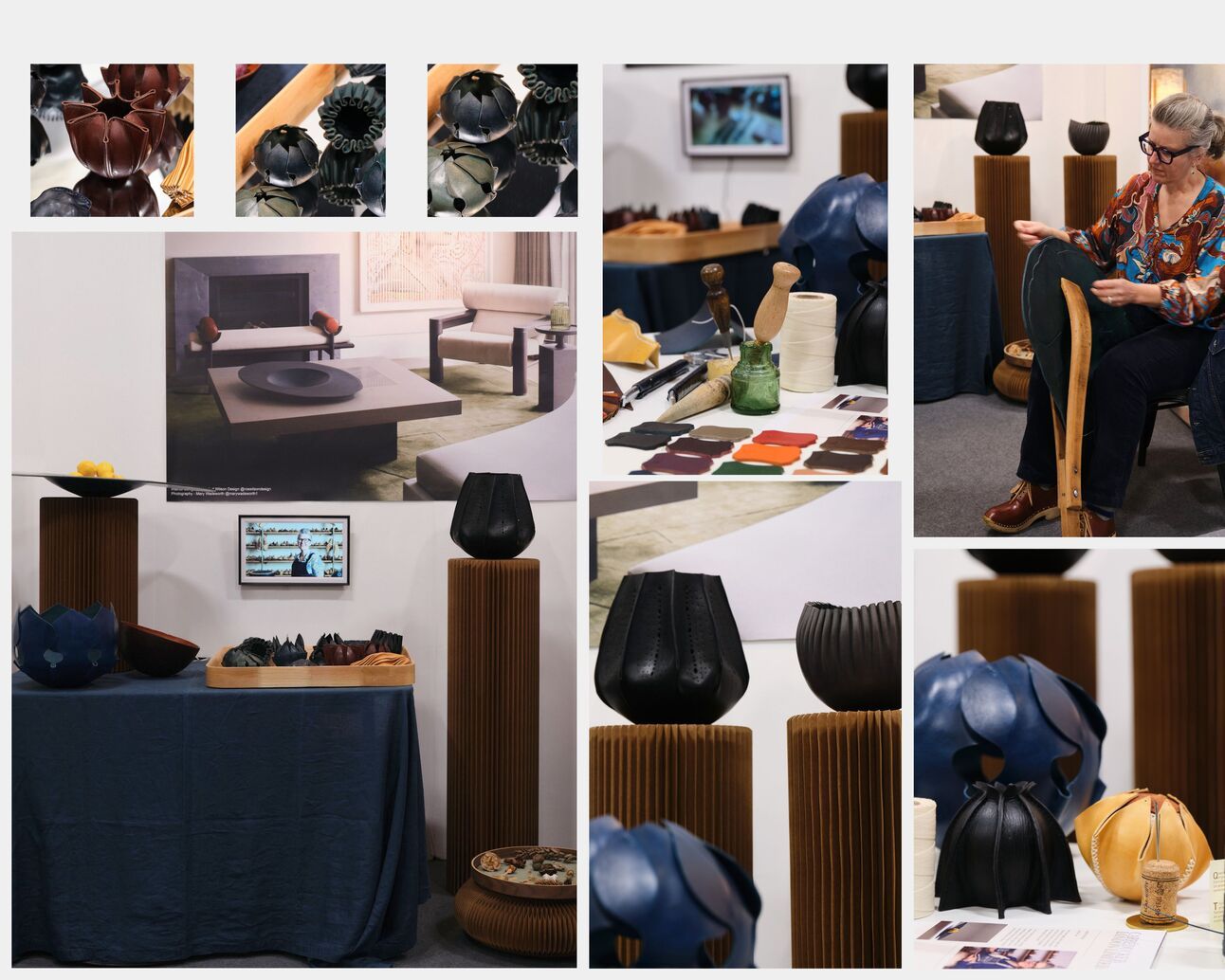
The stand at Making Spaces photographed by Yeshen Venema
Making Spaces is supported by Cockpit, QEST, Future Icons, The Black Artisans and Rycotewood Furniture Centre and has grown to become one of the highlights of the show.
There were 16 of us showcasing our work and process to thousands of visitors from stylists and journalists to interior designers, architects and lighting specialists. It was a fantastic opportunity and great to make so many contacts. Thank you!
In The Workshop
Recycling Shoes and Boots
Much as we love making new shoes and boots from scratch we’re always mindful of the wastefulness of footwear. So one of the things that we advocate is to look out for lovely uppers on second hand footwear. We then teach students in class how to rip down the footwear to rescue the uppers for them to remake on a new last.
It’s also a great way of giving a favourite old pair of shoes or boots a new lease of life or indeed a completely new look if the upper is still in good condition.
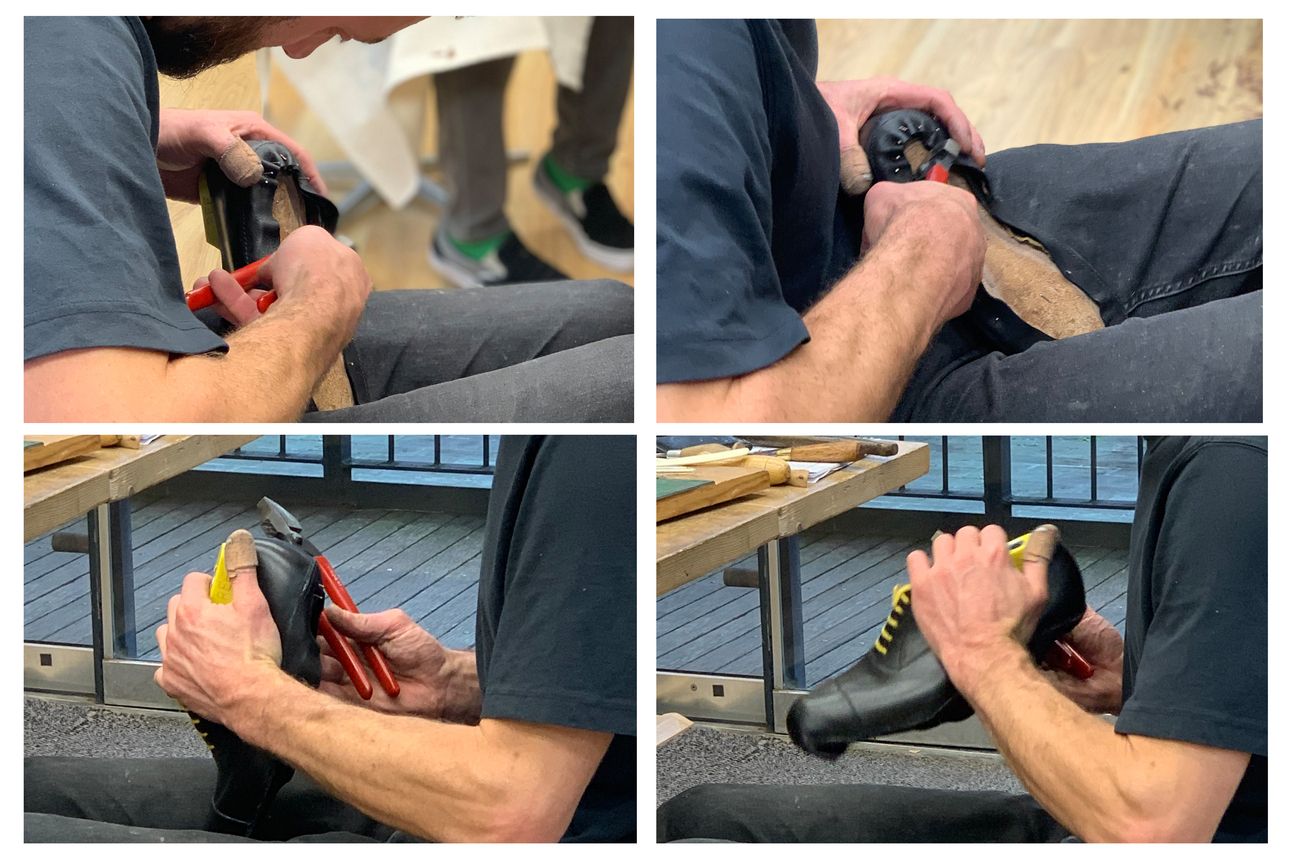
Ed easing the uppers over a new pair of lasts
We spent the last two days with Ed who’s up from Devon to learn Norwegian and Storm welting. He’s working on two pairs at once and we’re working with one pair of repurposed uppers, almost beyond saving, with very little lasting allowance and what was left, very fragile.
To strengthen the allowance we reinforced the edge of the lining with tape. Then we roughed up about 10mm of the surface of the upper around the bottom edge and cemented and then stitched a soft leather ‘skirt’ all of the way around. The patcher was great for this little job.
We soaked the uppers, (they were black so there was little risk of staining), mellowed them and then lasted them using the ‘skirt’ to give them a good pull down onto the lasts. It worked well and we were then able to cut away the ‘skirt’ at the heel and toe leaving the original upper lasted in place. Now any remaining cuts and knicks along the lower edge will be covered with the storm welt when it is sewn on.
We’ll be walking Matt through a similar process when he remakes this pair of apron fronted Todds bootees in Monday’s evening class.
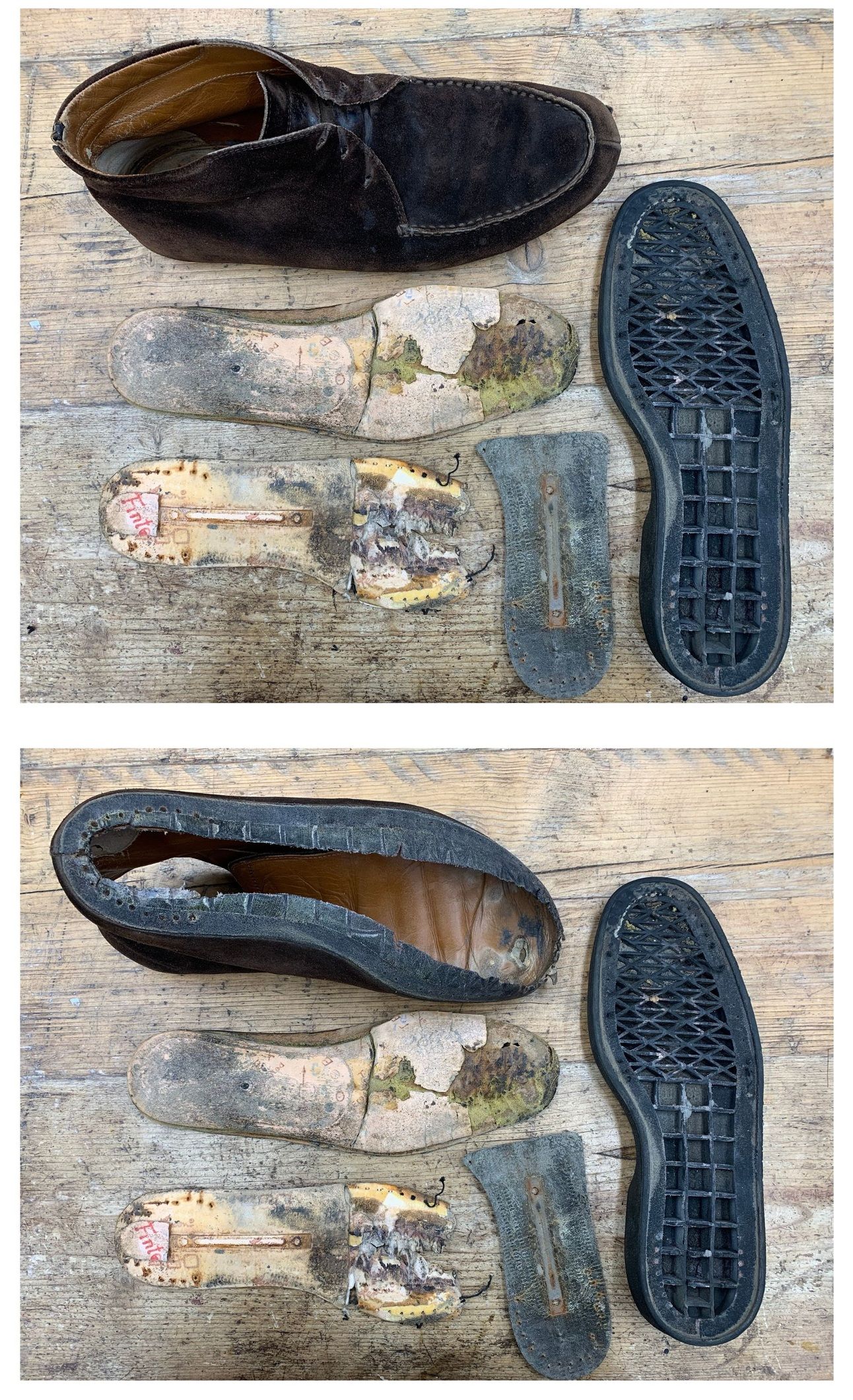
BESPOKE SHOE of the month
This month we’re doing a deep dive into…
THE LOMAN DERBY BOOT
The Loman is an example of our Bespoke Manufactured range - hand lasted, hand welted and finished by our specialist cobbler.
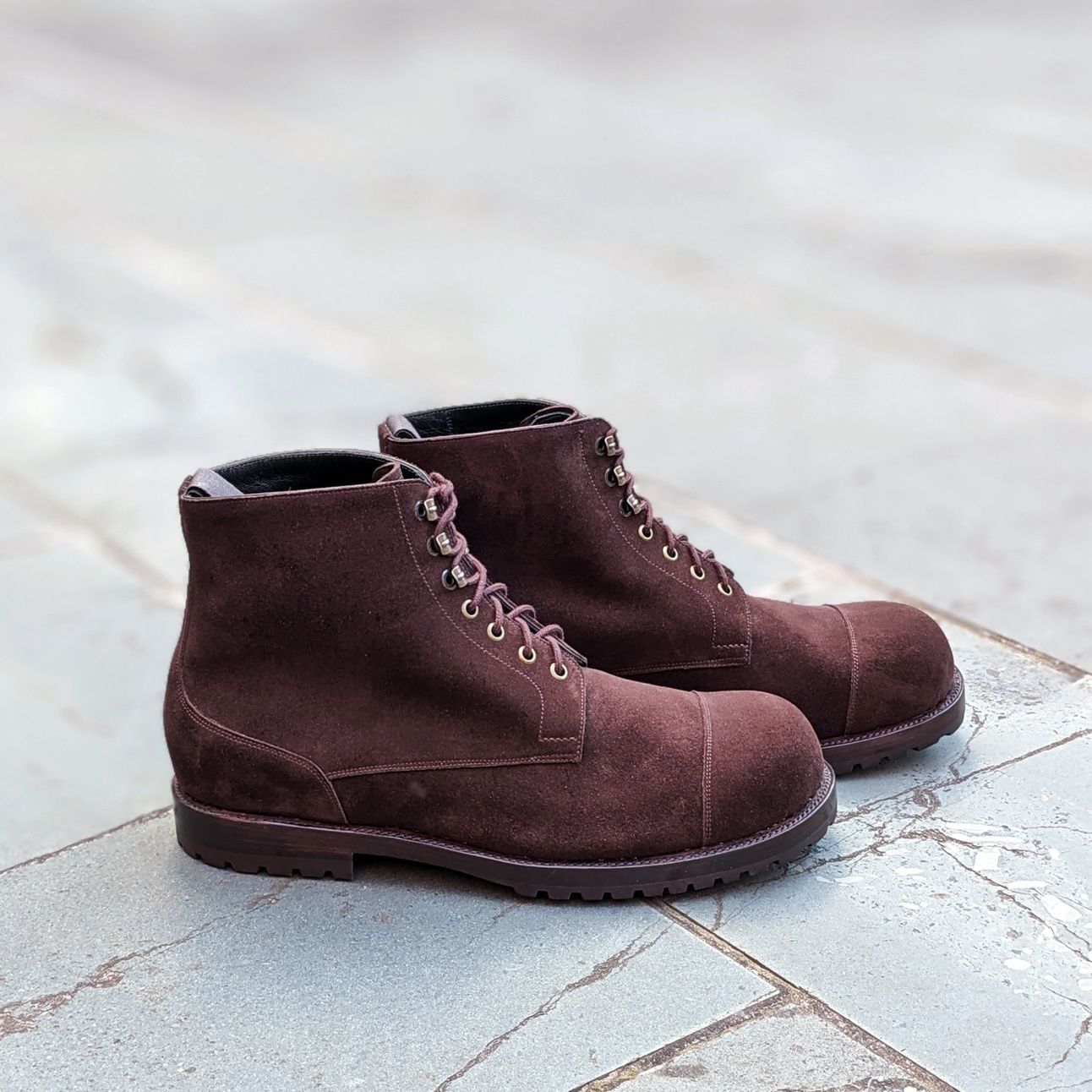
LASTS
The lasts are bespoke for a very special customer of ours. He had never had a pair of bespoke shoes before but it had been a lifelong ambition to have a pair. So after many years he finally took the plunge.
He’s in the building trade, and his style is relaxed workwear, so he chose a very round toe for his lasts with a high toe box to accommodate his large big toes.
STYLE
The style is a simple derby boot with a straight cap and counter; seven lace hole with eyelets and ski-hooks; canvas tugs; and with the counter overlaid on the quarters
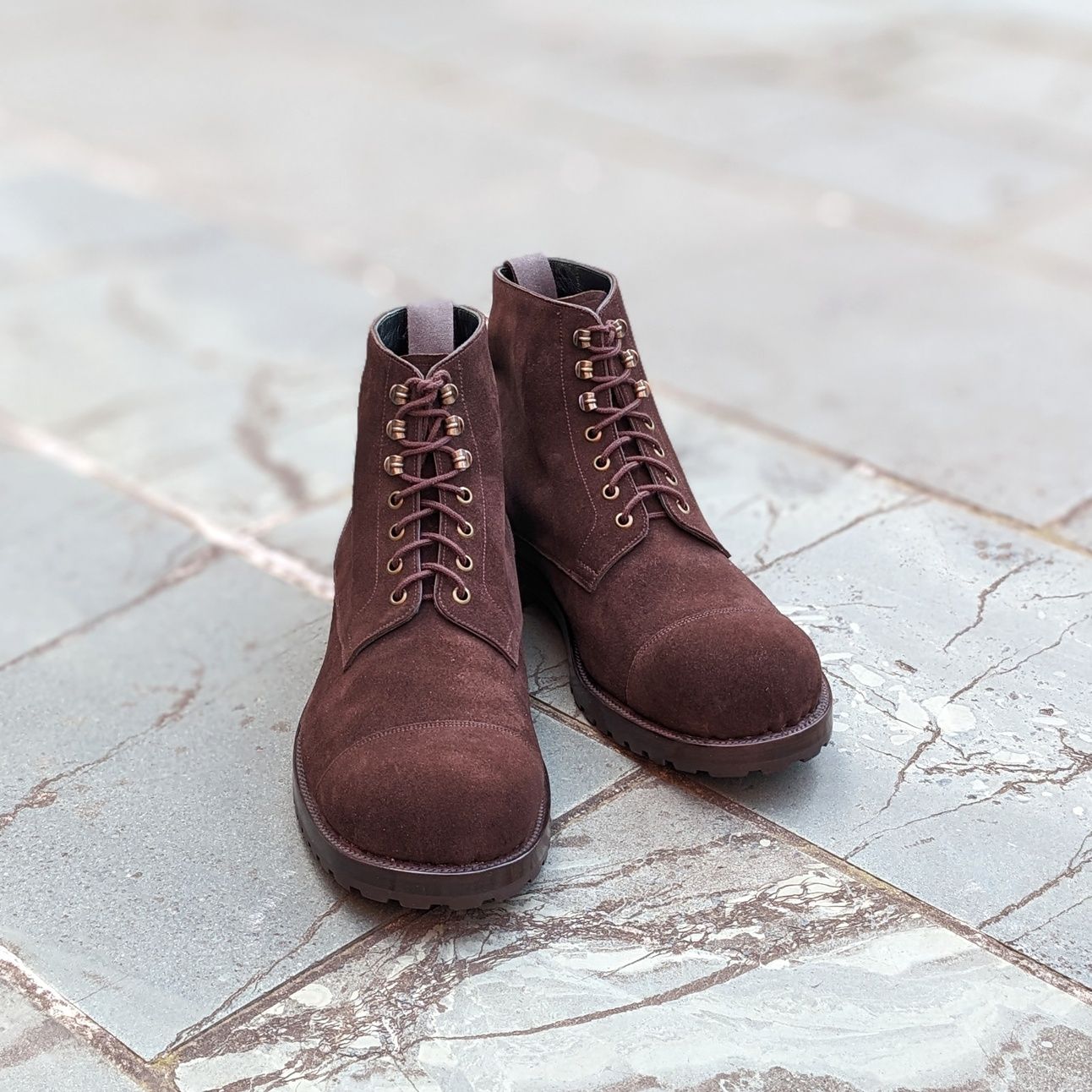
UPPERS
The uppers are made from a heavy, moss backed, chocolate brown suede made by Charles F Stead & Co in Leeds.
Moss backing is a process where resin is impregnated into the flesh side of the skin to make it more weather and stain resistant. This particular suede also has a type of Scotchguard added during the tanning which makes it the most durable suede we have found
And it’s British which we love.
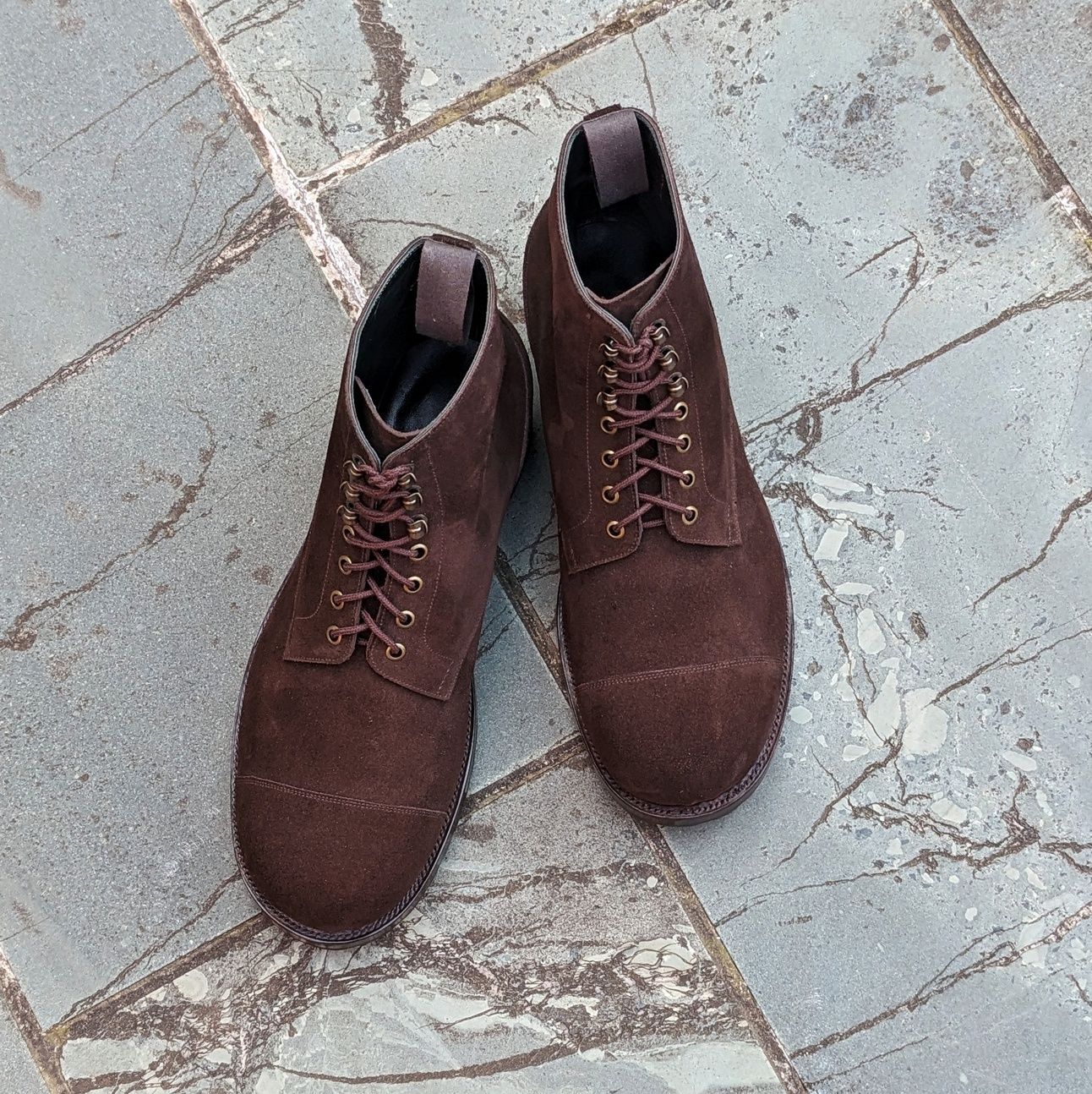
The lining is British Racing Green glace kid
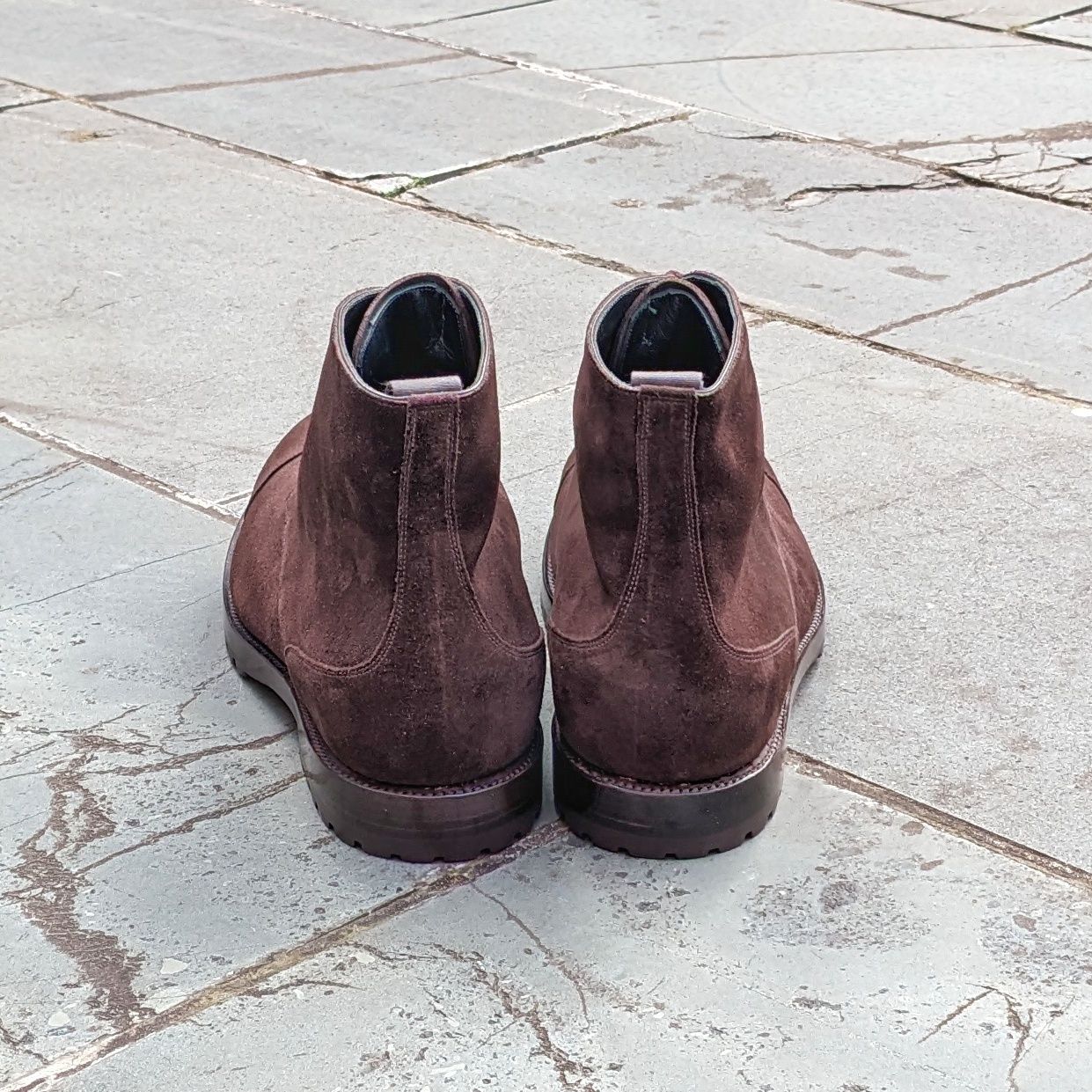
The counters have an integral backstrrap
MAKING
The Loman is made with the following features
1” heel height
6” back height
Welted seat which means the welt goes all around the back of the heel
3/8” sole thickness with a midsole
Machine stitched sole and heel unit
Commando sticker sole and heel top piece
Matching opaque inked finish with a high shine throughout
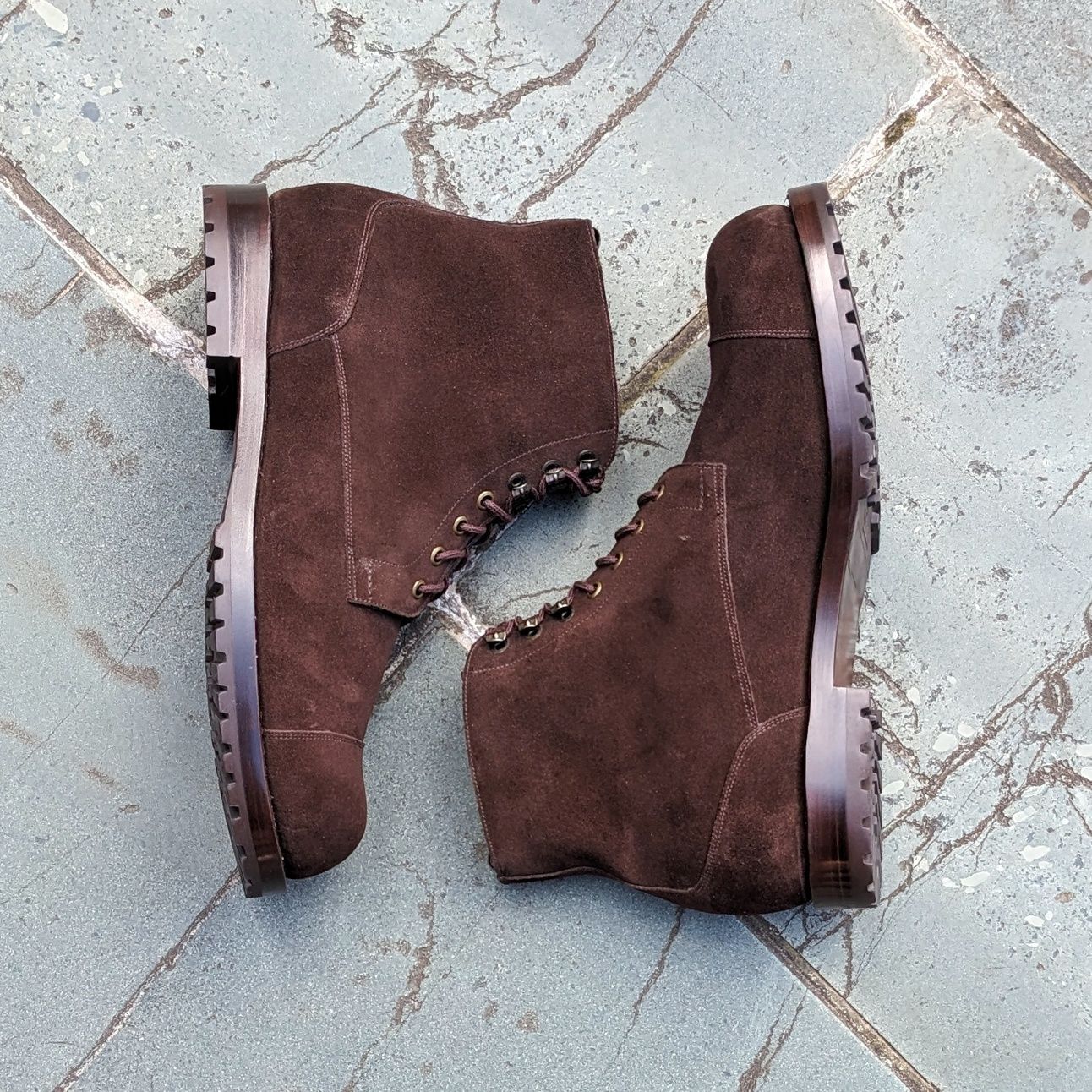
The commando sticker sole and heel top pieces
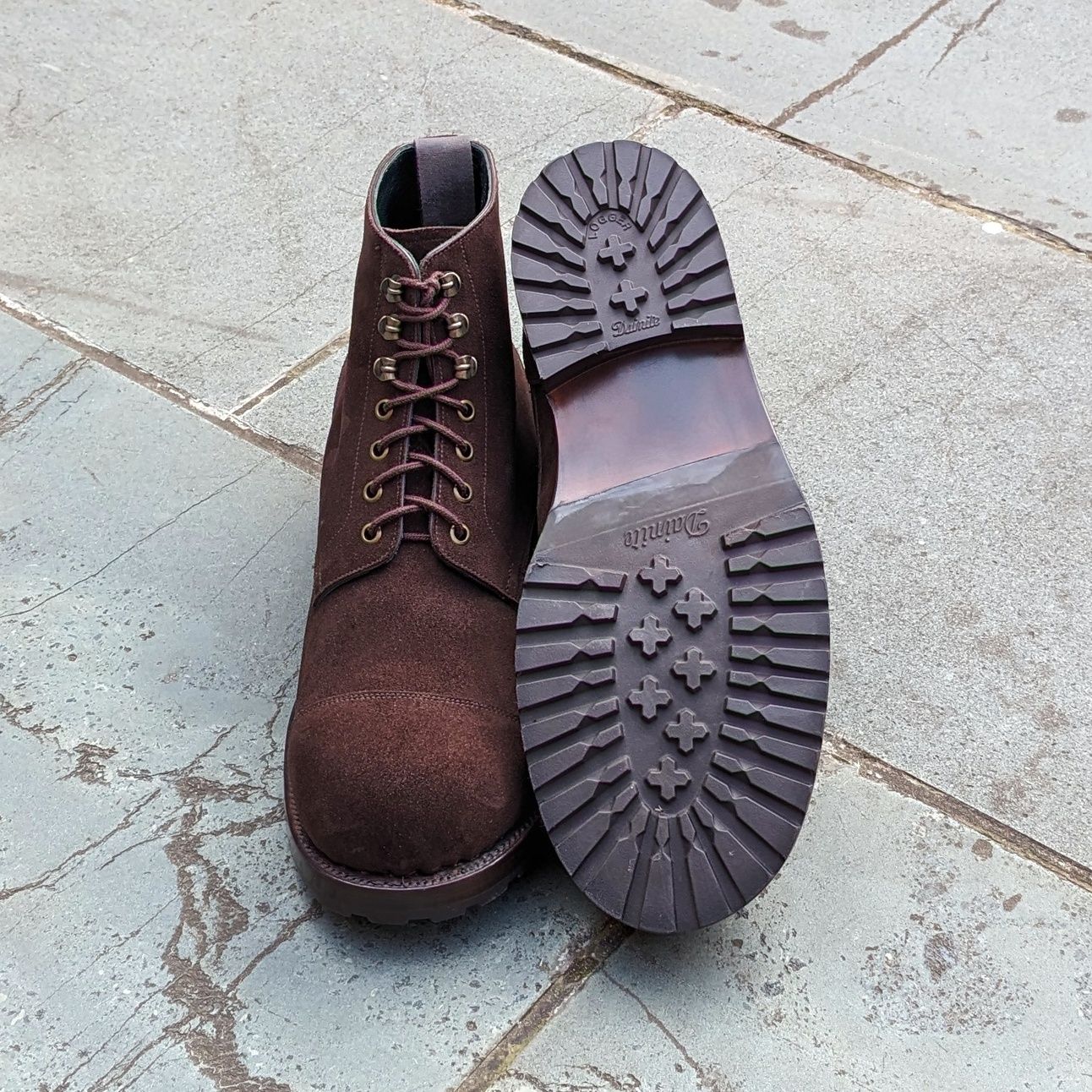
Tool Tips
New In The Toolshed
So, we have some shiny new tools in the Toolshed.
![]() Contour Gauge ![]() Short Handled French Hammer ![]() Thread Snips | First up is a Contour Gauge which is very useful for checking toe and heel shapes on lasts. And also on toe puffs, both the top contour and the side profile. Then comes a new French Hammer with a short handle, ideal for lighter work and those who want a lighter hammer. Small but with all the functionality of our other French hammers And last but not least, are these metal Thread Snips which are great for closing (making the uppers) on a post machine. High quality steel snips with very sharp blades |
To enjoy a 10% discount on one of these fabulous tools, click on the highlighted links above to go to the page, add them to your basket and then enter the code NEWTOOLS10 at checkout.
READ, WATCH, LISTEN
Reading: Hamnet by Maggie O’Farrell, fictional account of Shakespeare’s son Hamnet who died aged 11 in 1596
Watching: Alma’s Not Normal, an award-winning, near-perfect British comedy-drama by stand-up Sophie Willen; heart-breaking and hilarious in equal measure.
If you know someone who would enjoy The Journal please copy and share the link below with them.
We promise to publish once a month, not to share your details with anyone and to try to make sure that there’s something of interest for you whether it’s new shoes, tools, materials, events or projects.
And if there’s something you’d like us to include, please email us with your suggestions [email protected]…what would you like to hear about?
Many thanks
Deborah & James
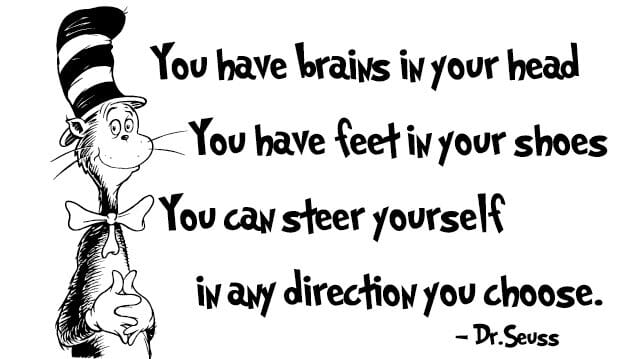