- Bespoke Shoes Unlaced - The Journal
- Posts
- Journal : Issue 2 : Coad Conference Clogs
Journal : Issue 2 : Coad Conference Clogs
A monthly glimpse into our shoemaking world
JOURNAL 2
COAD CONFERENCE CLOGS
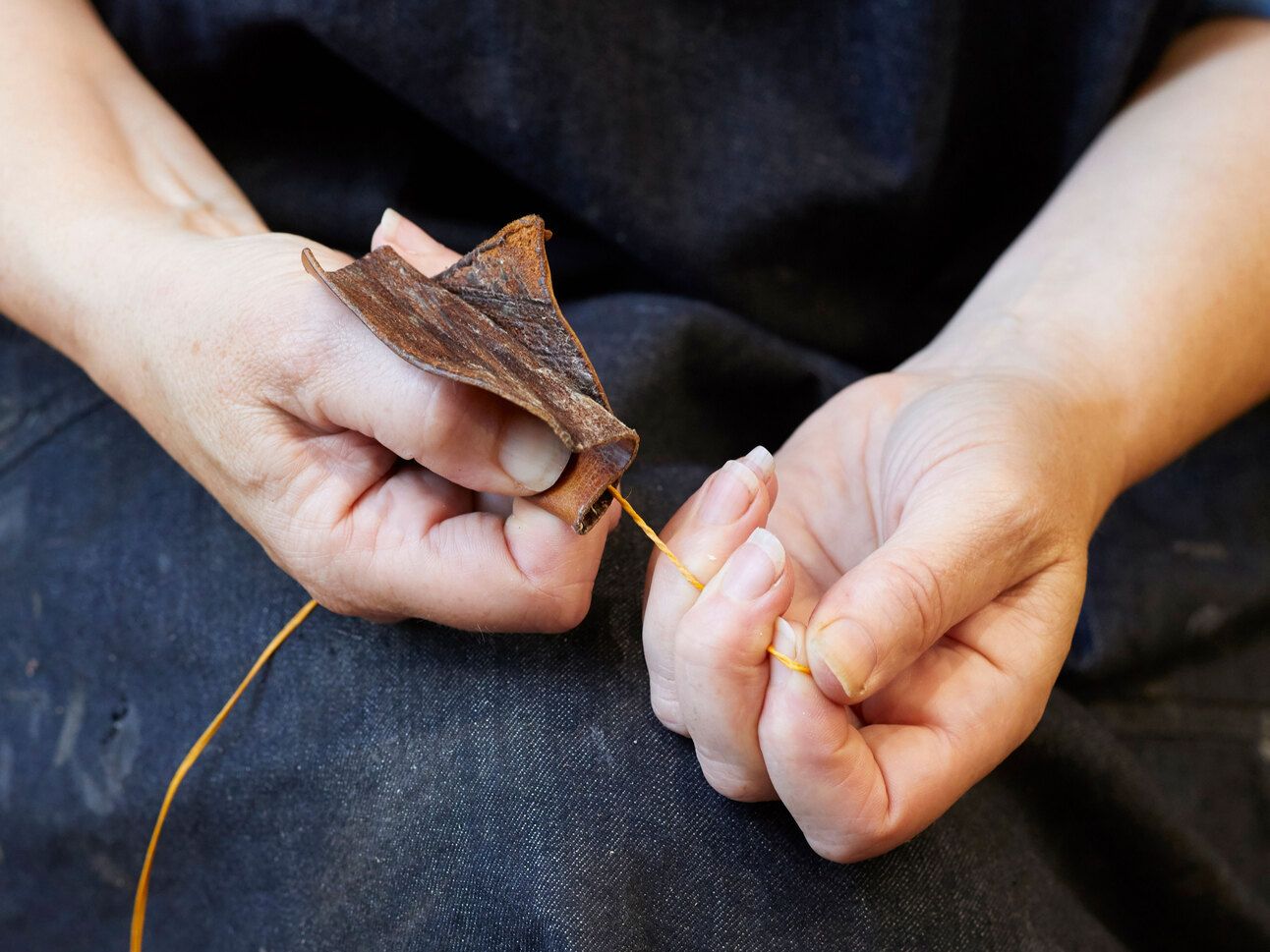
COAD - The Secret Ingredient
If you’re new to handsewn shoes as either a customer or a maker, you may be wondering what all the fuss is about, when it comes to shoemaking thread? Well, it is in fact, one of the things that sets handsewn shoes apart.
The threads we use are made by waxing and twisting lengths of linen thread together. The coad or shoemaking wax, is the secret ingredient.
We then use a pair of bristles or needles to hand sew the welt to the shoes and to stitch on the sole. This is where the waxed thread really comes into its own. As we pull the threads through each hole, fast, the wax warms up, allowing the threads to glide past one another.
Once we’ve made and tightened a stitch the wax cools, sticking the two threads together to form a plug. The benefits are two-fold, the wax holds the tension on each stitch and the plug holds the layers of leather together, so even as they wear through the sole stays securely attached.
Watch our Breaking Bad themed video on YouTube to discover more and
INDEPENDENT SHOEMAKERS’ CONFERENCE
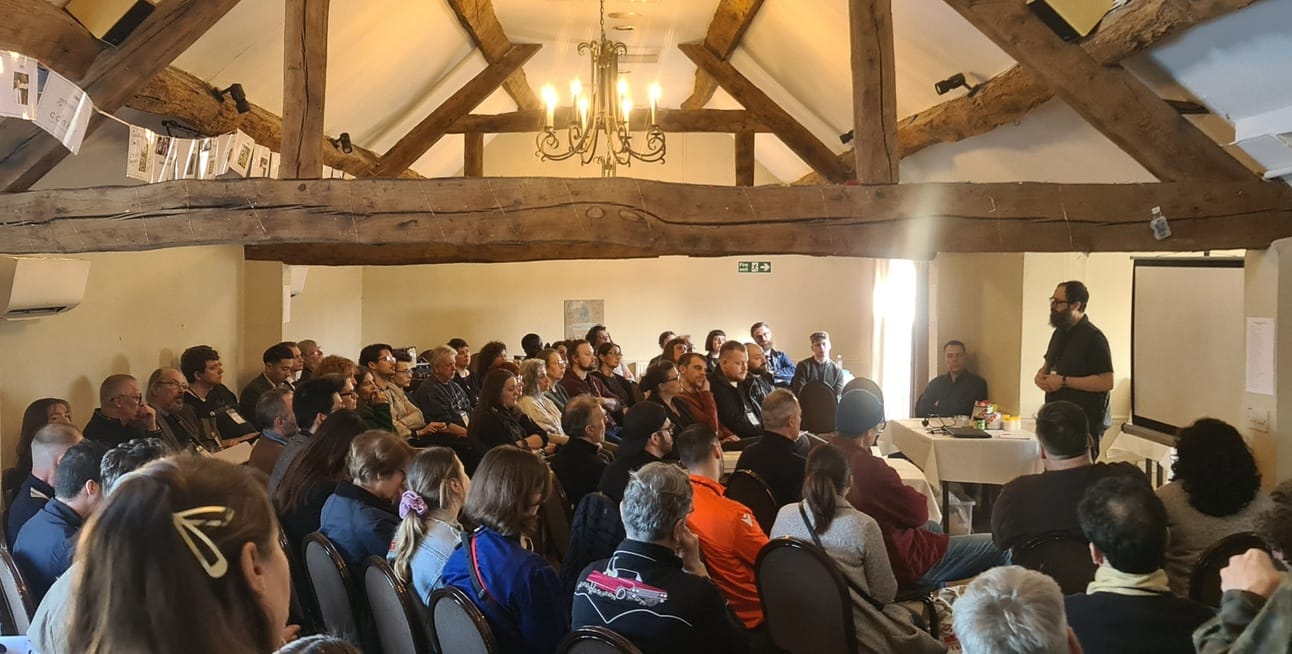
What do you call a room full of shoemakers?
This year’s conference in leafy Warwickshire, was meticulously organised once again by the team at Bill Bird Shoes. They experimented with a new format with a variety of different, smaller masterclasses running simultaneously, interspersed with longer talks. It was a really vibrant atmosphere and meant we could all dip in and out of lots of different specialist areas from thread making and tool renovation to orthopedics and shoe polishing.
We were delighted to deliver a masterclass on making shoemaker’s thread wax or coad as it’s otherwise known with a presentation and live demo.
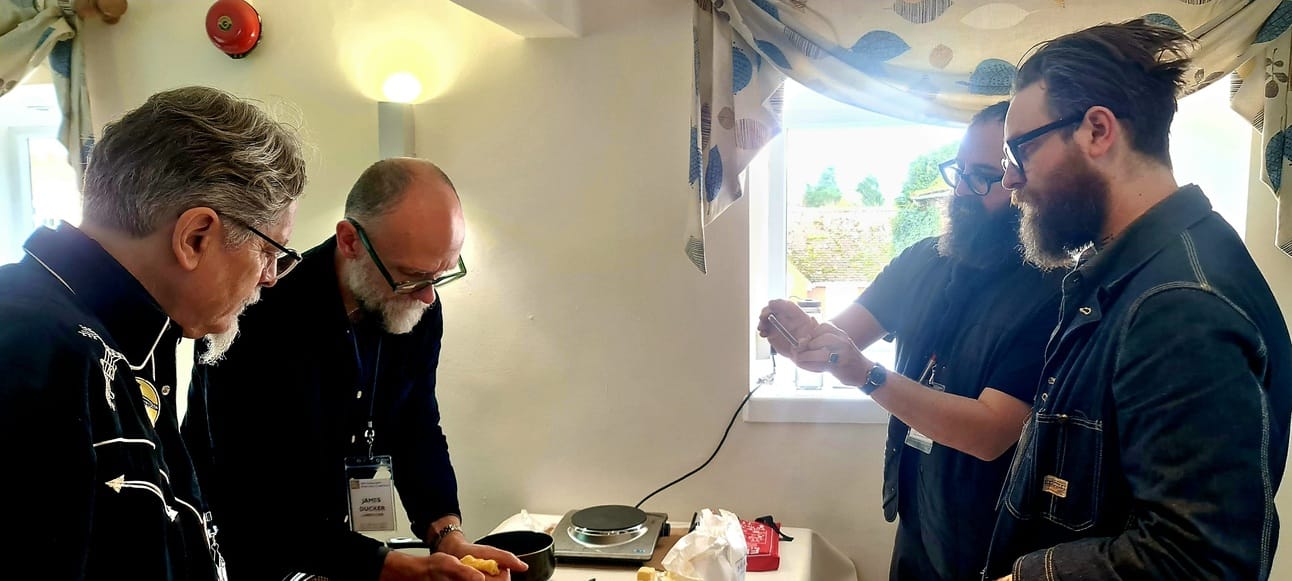
Extensive ‘beardage’ as Dominic Casey, Sebastian Tarek and Thomas Rowe watch James cooking coad
![]() Mariano Crespo and Trickers’ bespoke shoemaker Adele thread making masterclass ![]() ![]() William Laborde showing how to renovate old tools - the oldies are the best | ![]() Hartmut Seidich from Germany sharing his orthopaedic expertise on fitter uppers ![]() ![]() Anders Sundstrom, with a rapt audience as he demonstrates glacage |
There were also materclasses from Samuel Norsworthy of Catella Shoemaker demonstrating Patina, Stefan Hustadt from Renia Adhesives and Bill Bird generously sharing his extensive knowledge on last fittings.
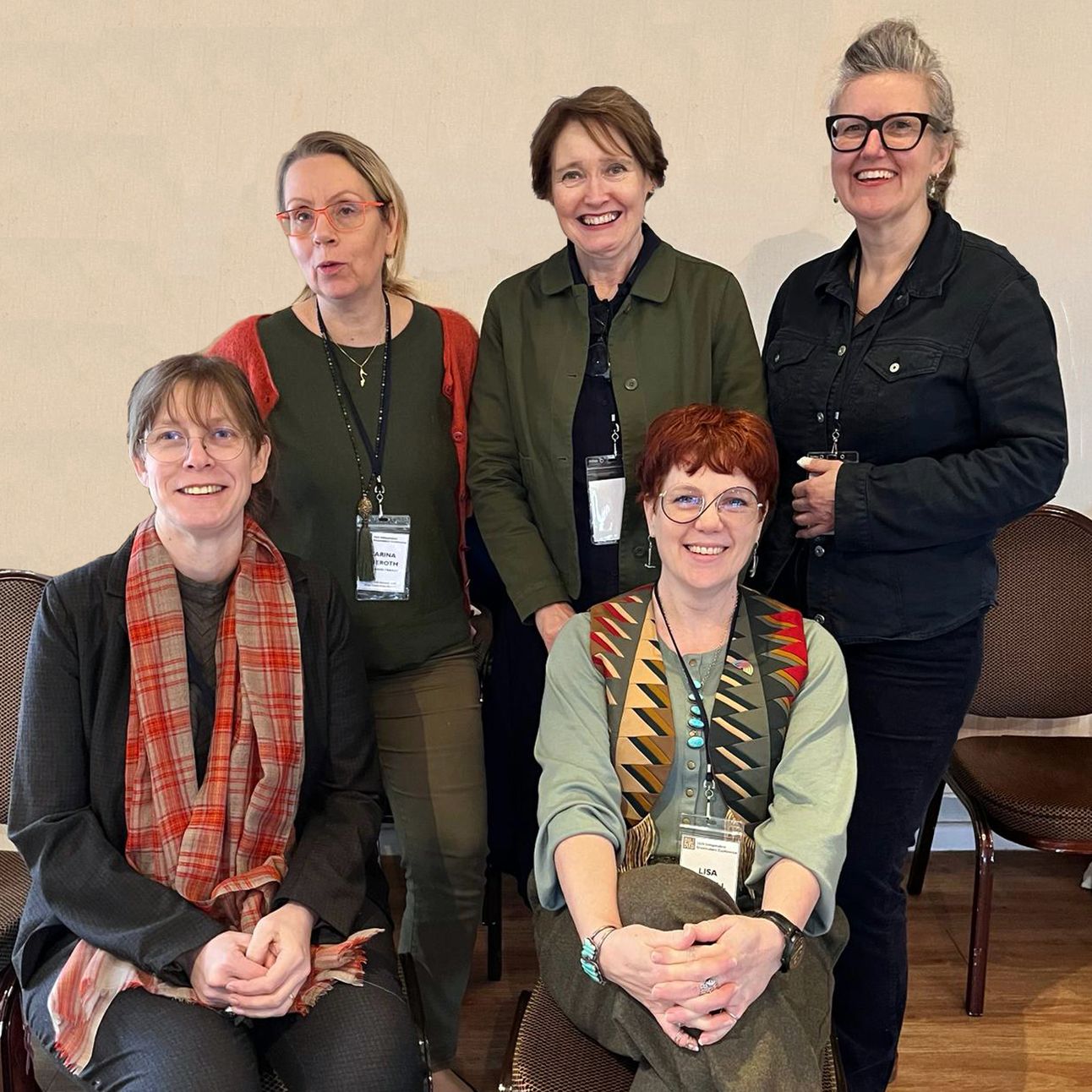
An international flavour: Anna and Carina from Stockholm, bespoke pattern specialist Fiona Campbell and yours truly from London and cowboy boot maker, Lisa Sorrell from Oklahoma USA.
And the finale was a talk by Thomas Rowe, a generous, heart warming insight into the world of making footwear for the film industry. It was great to see some of the pieces he and his team have made and top hear about the challenges of working to tight deadlines and creative briefs.
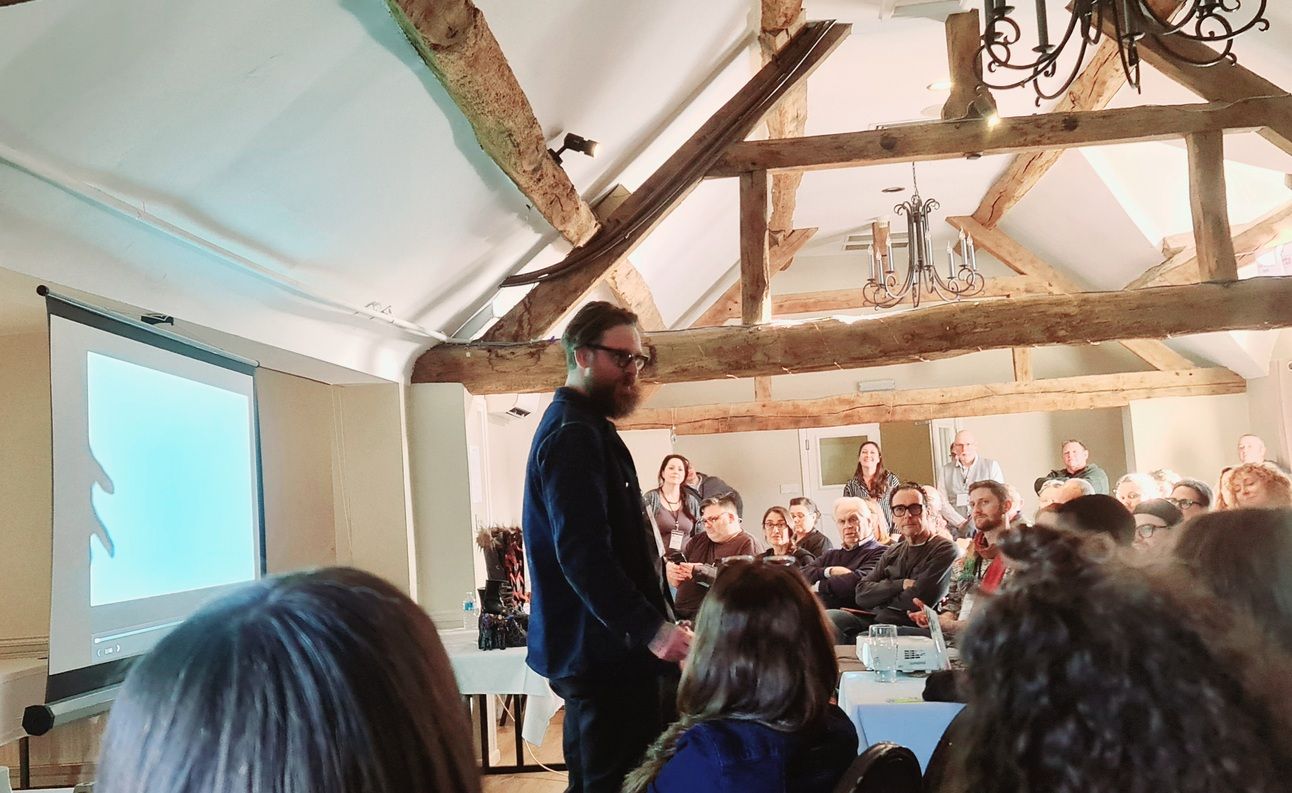
As always a grand day out, spent with a great group of makers.
Until next year…
BESPOKE SHOE of the month
Lavington Derby Boot

This month’s favourite boot is one of the most recent bespoke orders we have delivered - The Lavington Derby Boot
THE STYLE
It’s a low derby boot with a straight toe cap and heel counter. It has extensive 2:1 brogue punching on the seams; hand stay stitches; and 4 laceholes with antique brass eyelets.
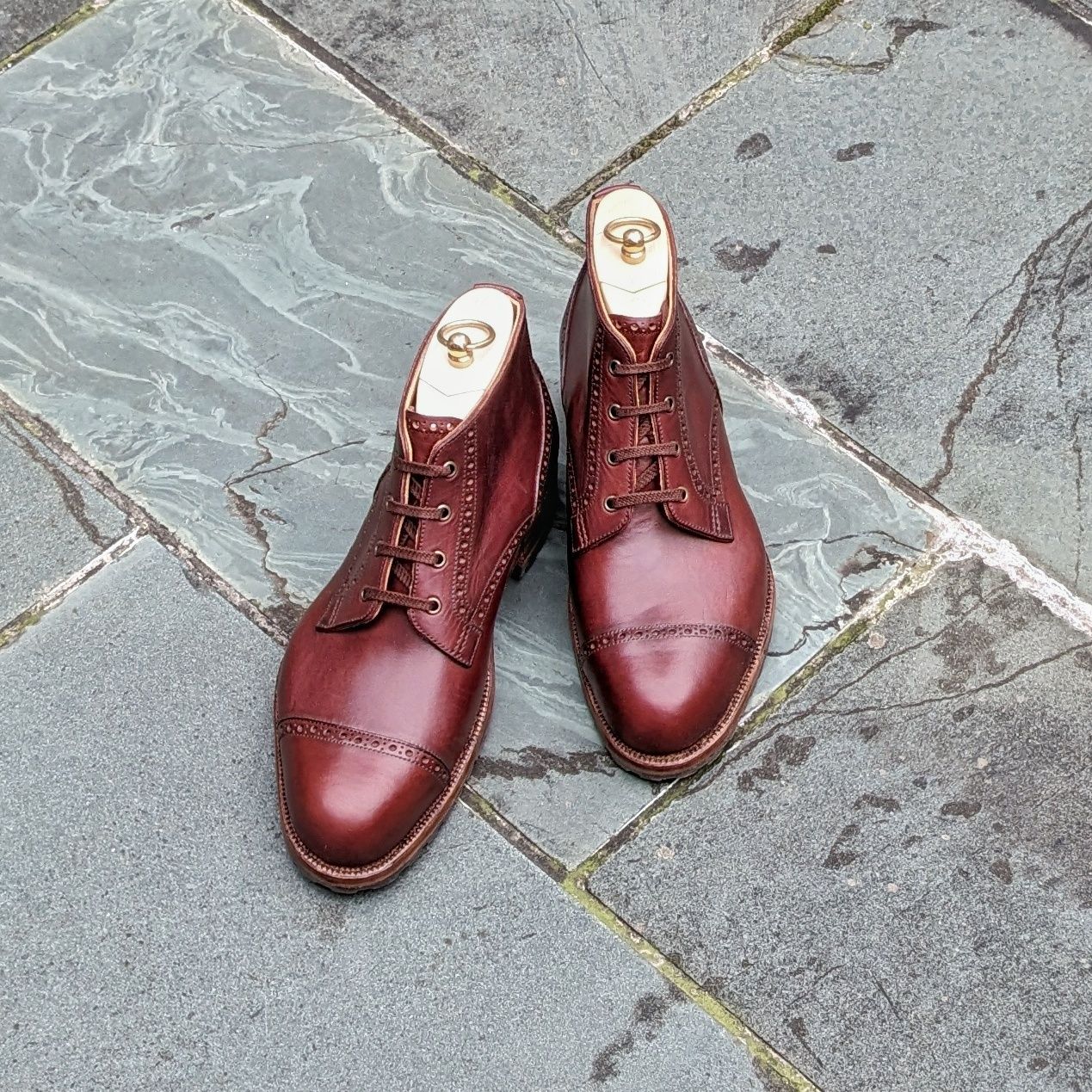
The Lavington
THE SHAPE
The boots have a soft almond shaped toe and a wide joint (widest part of the boot). As with all bespoke lasts, the shape is a reflection of the customer’s foot measurements.
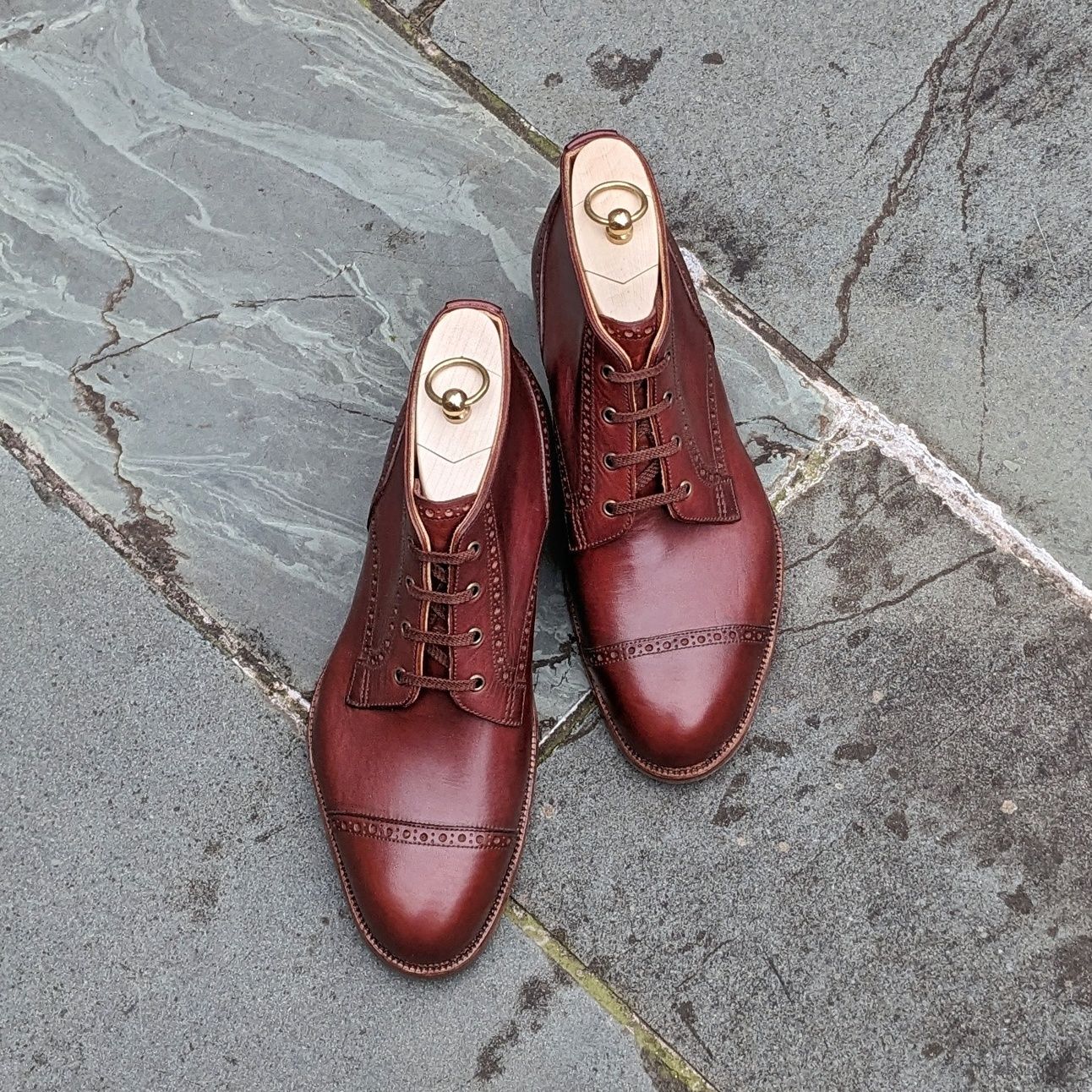
THE DETAILS
We love to play with classic shoe detailing and we did this in two areas of the boots. The first is on the heel counter where the two lines of brogueing merge to form a single line up the back. As you can see, our closer did a fantastic job with this.
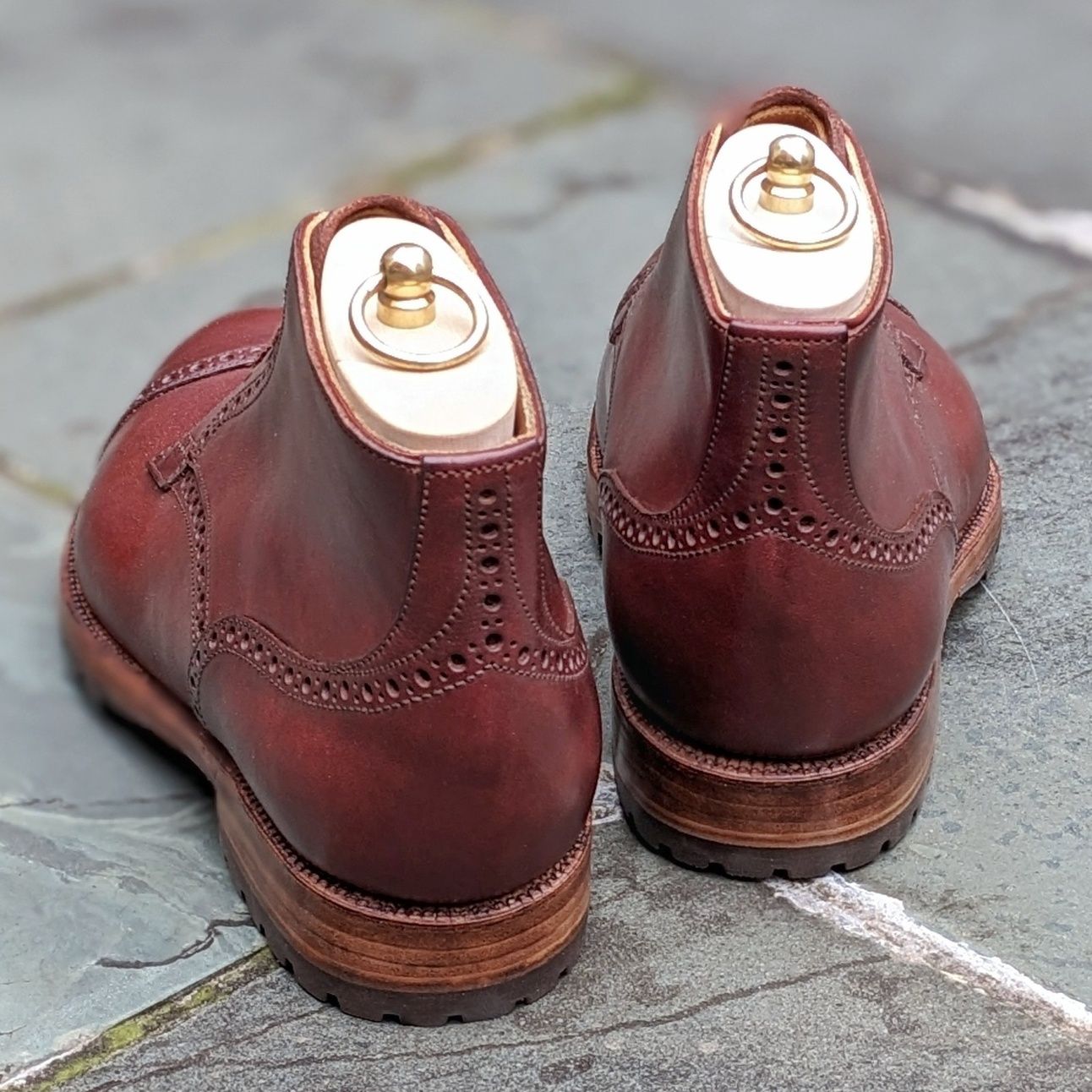
Bespoke Punching Detail on the Counter
The other addition is a little tab at the end of the facings which allowed us to add a line of brogue punching on the “wrong” side of the seam.
The thickness of the leather (1.8-2mm) means the brogue punch holes have a 3D depth which we love
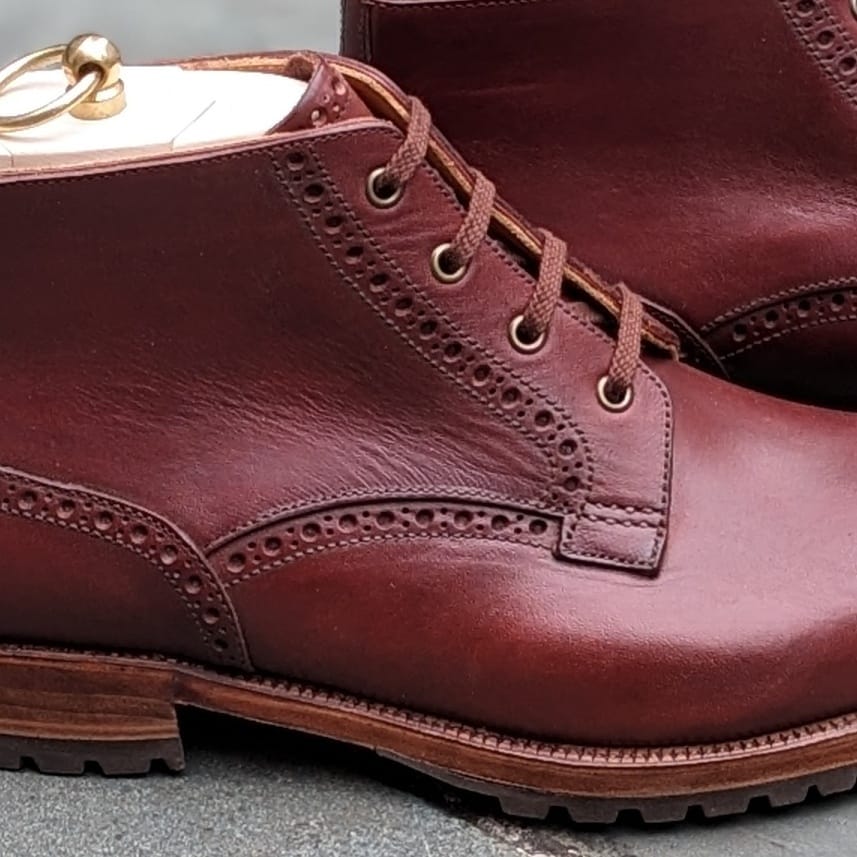
Tab On The End Of The Facings
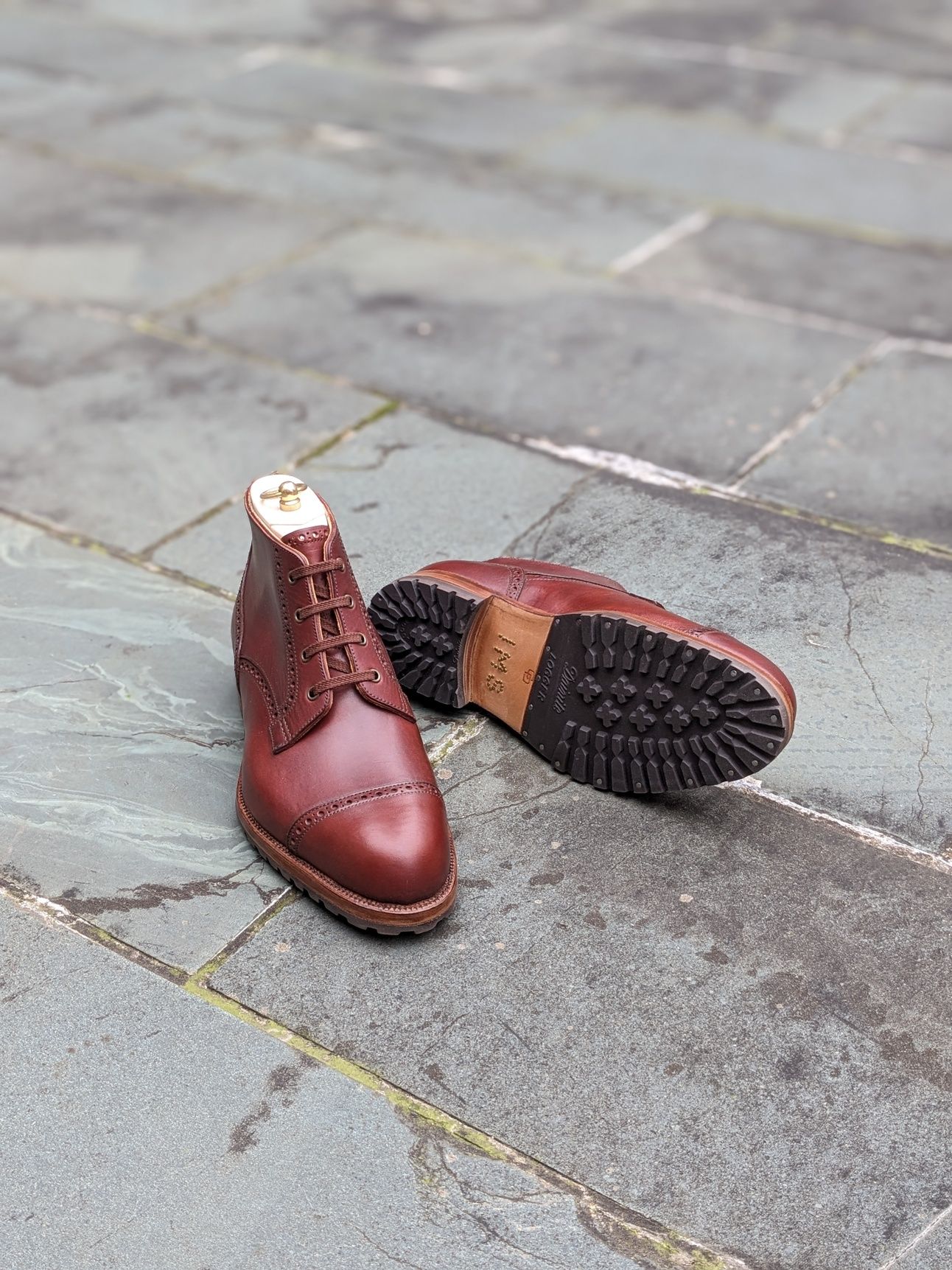
The customer’s initials are on the sole in brass nails
THE LEATHER
The uppers are made from veg tanned leather by Italian tannery Tempesti. We increasingly use veg tanned leathers because they are tanned in a much more sustainable way than chrome tanned leather. They use vegetable tanning agents and vegetable pigments in the production. The resulting leathers are slightly heavier than classic box calf.
But the thing we love about them most is the depth of colour and the life you can see in the grain of the leather. They also age beautifully, developing a deep patina and subtle colour variation over the years.
The lining is a veg tanned calf in our classic straw colour
All of the other leather components (soles, insoles, heels etc) are oak bark tanned cow hide by Bakers of Colyton, Devon, one of only two pit tanneries left in the country. Their leathers take 12 months to tan and are well worth the wait. They’re great to work with, durable and and sustainably produced.
THE MAKING
The key construction features of the Lavington are
Hand lasted
Hand welted
Welted seat (the sole stitching goes all the way round the heel for a more robust look)
Hand stitched leather sole with midsole
Hand built stacked leather heel
Commando sticker sole and heel top piece
Initials in the waist made with brass nails
Hand finished with natural sole and heel edges
Heritage British Clogs

Filming Phil in action for the Kickstarter campaign
Launching soon is our latest Kickstarter campaign. We’ve done three successful campaigns over the years and this time we’re shining a light on heritage British clogs.
Our clogs will be made up in Yorkshire by Phil Howard. We’ve been wearing his clogs for a while now and love them. They’re super-comfy, great for your feet and we think they look cool!
The beauty of a kickstarter is that we take pre-orders for the clogs and then only make the number of pairs of clogs that we need, so there is zero waste.
If you’d like to find out when the kickstarter goes live, please drop us an email [email protected] and we’ll be sure to let you know.
Tool Tips
April’s tool of the month is the humble bristle, particularly these steel bristles which are newly for sale on our website
TOOL - BRISTLES | TECHNIQUE |
![]() Metal Bristles | What is a bristle? A bristle is a flexible needle attached to the end of a sewing thread. They have a point (these have a blunt point) at one end and an eye at the other They can be made of metal, nylon or natural boars’ hair |
![]() The Eye | Why are they called bristles? Originally they were made from the long, thick bristles on the back of a boar’s neck which they raise when threatened or fighting. |
![]() The Blunt Point | How are they used? They are attached to the end of a sewing thread and are used when a straight rigid metal needle will not work well - usually when the hole to be stiched is through a thick material like leather or when it goes through a curved hole. Or both. In these cases, you need something that is either flexible (boars’ bristle, nylon) or semi-flexible and curved (metal bristle) |
![]() Metal Bristles | These bristles are straight but we put a curve into the tip which matches the curve of the awl being used for each job. We also use nylon bristles which can be made from fishing line (0.4 - 0.6mm gauge) |
![]() Attaching a Nylon Thread | How are they attached? It depends on what kind of thread you are using. If it’s a nylon thread, you can attach them much like a needle for saddle stitch - by making two holes in the thread and passing the bristle through each one and pulling tight to lock the bristle in place. |
![]() Attaching a linen thread with tar | If you are using a handmade linen thread, tar the tapered end and pass the tip of the thread through the eye of the bristle and twist. The tar will hold the bristle in place. |
OFFER
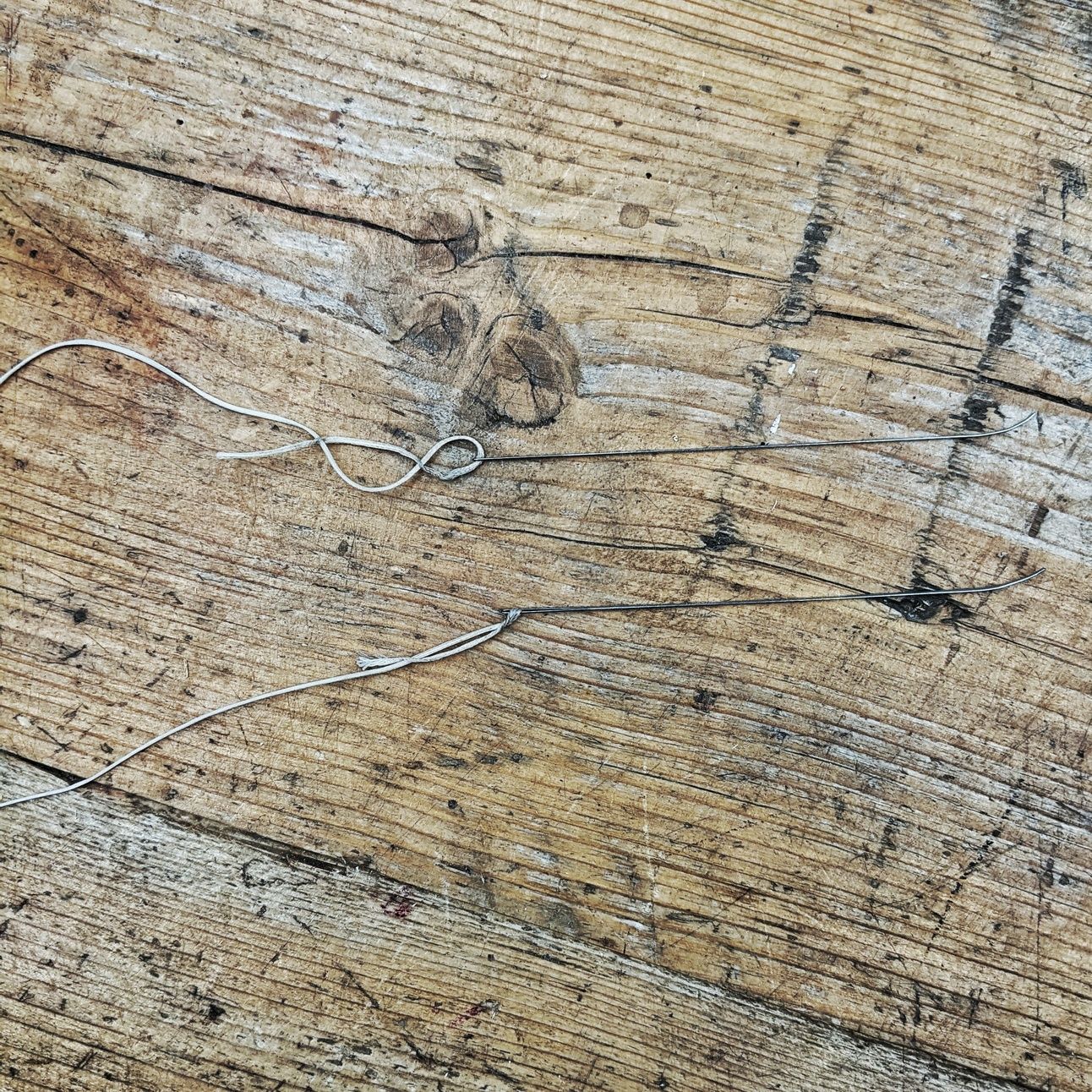
To enjoy a 15% discount on metal bristles hit the link below and enter the code BRISTLES24 at checkout.
WHAT’S ON NEXT MONTH
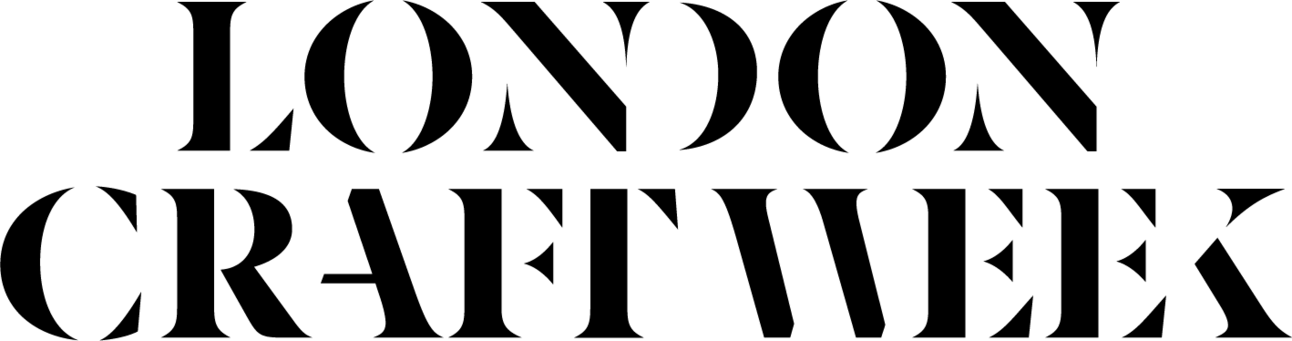
A NOVICE APPROACH exhibition
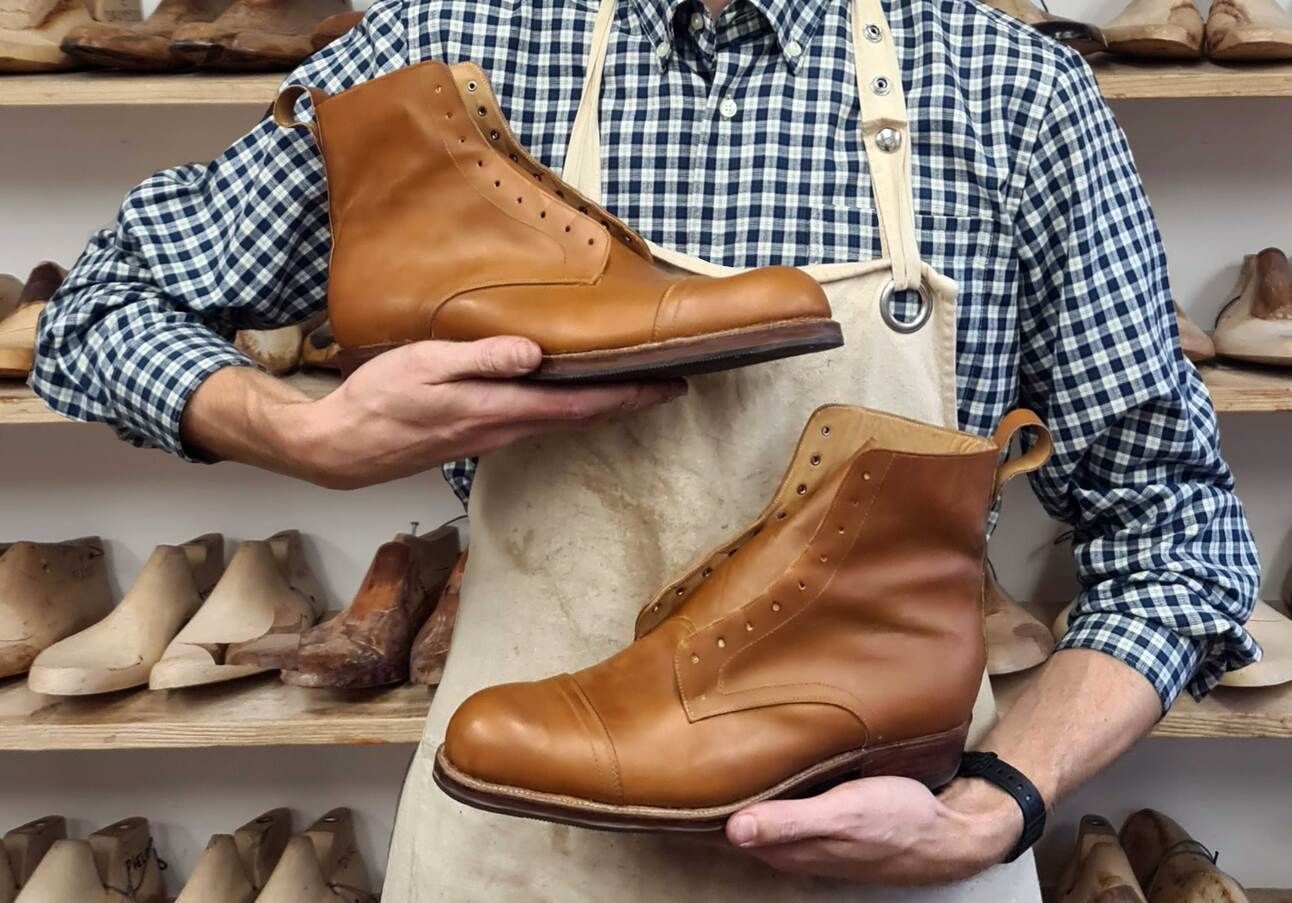
Unit 1.20 Oxo Tower Wharf
13 - 17 May 10am - 5pm
We’re hosting an exhibition of student shoes and boots next month during London Craft Week 2024. If you’re in London, please pop in to see some of their amazing work, showing just how versatile handsewn shoemaking can be.
COAXED exhibition
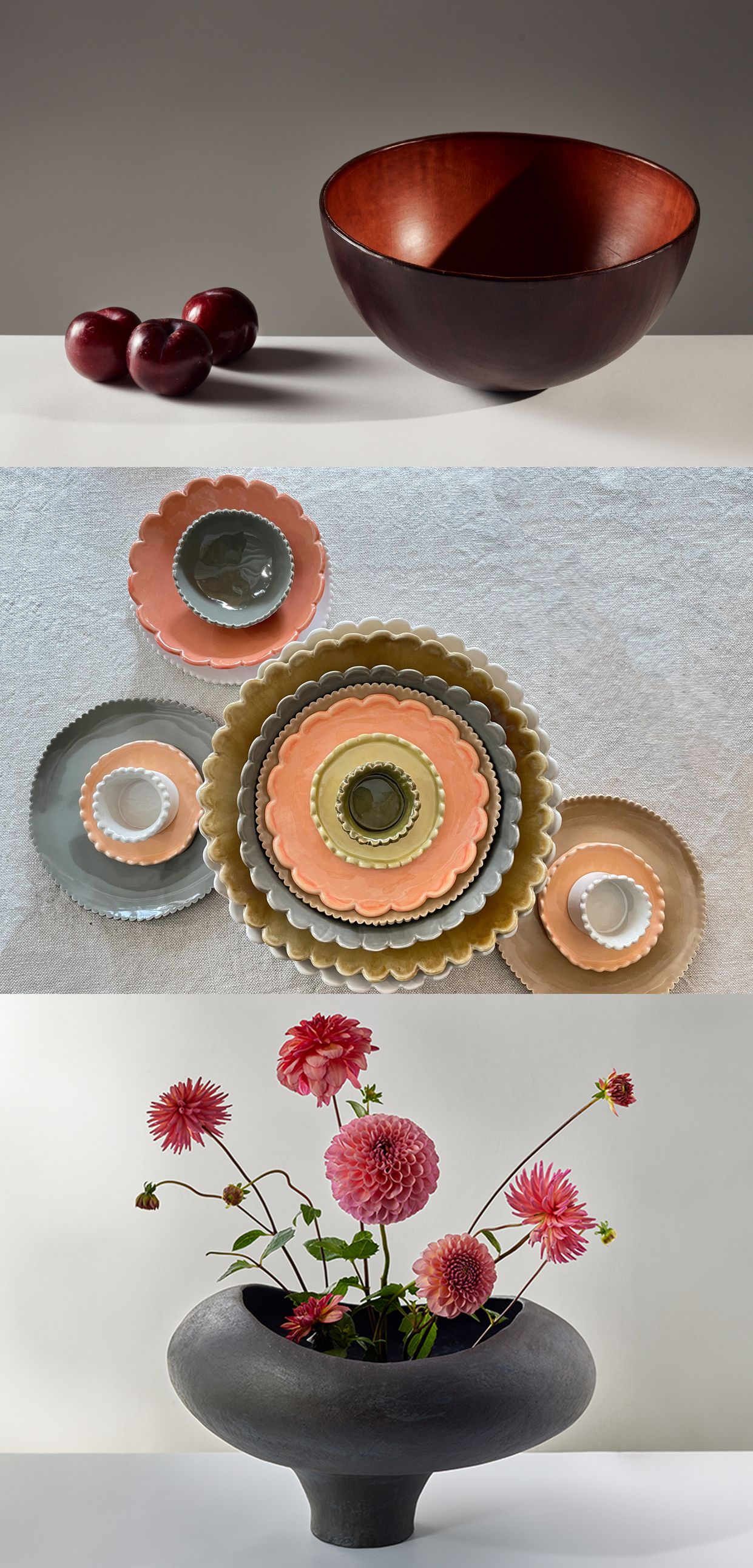
13 - 18 May : Monday - Friday 1 - 6pm; Saturday 1 - 8pm
Visit Unit 1.22 Oxo Tower Wharf to see our new molded leather work alongside By Raffaella and KCHPottery.